20 YEARS
TO 12 WEEKS
British manufacturers unite to build ventilators for the NHS
As we all have experienced, the COVID-19 pandemic truly changed how we work, live, and communicate. However, back at the start of the year, no one could have predicted the wide-ranging effects the virus would have on our communities.
Emerging from these times are stories of people coming together to help. While we were socially distanced, we came together to support each other. Neighbours helped others get shopping. People moved to their doorsteps to clap for key workers. And an extraordinary group of British organisations came together to support the government and help produce critically needed ventilators.
Back in March, it became clear to the government what the true scale of the COVID-19 pandemic could look like in the UK. COVID-19 affects the lungs, requiring use of ventilators to help manage severely ill patients. At that time, there were only 5,900 ventilators available within the NHS. This was around 20,000 ventilators short in a worst-case scenario for the NHS. And at the time, the UK had no local manufacturing base for ICU ventilators. Global demand meant that importing ventilators through established overseas suppliers was unlikely. It was clear that to meet demand, it would require a national effort.
The UK government launched its 'call to arms' asking British industry to help produce critical ventilators.
An urgent government request
In a briefing to over 100 UK manufacturers, the government made a formal request for help to start producing ventilators to support the NHS. Dick Elsy, the CEO of the High Value Manufacturing Catapult offered to help co-ordinate industrial support. So, he started to make calls. Just three days after the briefing, a consortium of nine UK industrial, technology, and engineering businesses from the aerospace, automotive, motorsport, and medical sectors officially came together. This was the start of Ventilator Challenge UK consortium. By the end, it grew to include many more businesses.
This consortium brings together some of the most innovative companies in the world. Every day, their highly skilled staff collaborate to create solutions that help millions of people, and this project is no different. They are working together with incredible determination and energy to scale up production of much-needed ventilators and combat a virus that is affecting people in many countries.
Uniting with a common goal
Faced with a major challenge, these organisations, often competitors, all had a common goal:
To build at least 20 years' worth of ventilators in 12 weeks because every ventilator built has the potential to save a life.
This shared purpose saw all these companies, with incredible determination and energy, come together. Every ventilator built would have the potential to save a life. With the help of tools and technology to enable collaboration, the Ventilator Challenge UK consortium was able to work together both selflessly and effectively. Most importantly, when you work together with trust and openness, you can achieve amazing things.
Microsoft Teams
Consortium members used Microsoft Teams to meet and share information in a secure place across all the organisations.
It allowed them to share intellectual property while keeping it protected within channels. Members could easily chat, have meetings, and hold live training sessions across all the organisations remotely. Having had no prior experience with using Microsoft Teams the site was set up in a day and in little more than a weekend it had over 600 users using it as the main tool for collaboration across the consortium. Given that most of the users had no experience using Teams, this almost instant adoption would not have been possible had it not been such a user-friendly and multi-functional platform.
It's astounding to think that for several weeks of the ventilator project many of us had not met face-to-face and only over the virtual medium of Microsoft Teams. It's been a rapid education in how it can make our teams more effective and efficient and we see the positive impact it can have on our businesses going forward.
Two ventilators, two programmes
Led by a coalition of leaders from the principal businesses, the consortium met regularly via video call, often day and night. This helped them stay aligned, coordinated, and laser-focussed on their objective.
They decided to support existing manufacturers to rapidly scale up the manufacture of existing ventilators as this would allow them to produce more ventilators quickly.
The Smiths paraPAC plus™ ventilator was tried and tested, but to scale-up UK production to the level needed to support the NHS and Government in the timeframe required, extra capacity was needed.
The consortium was also approached by the government to similarly mobilise around a ventilator concept from Penlon. The Penlon ESO 2 Emergency Ventilator modified existing proven clinical equipment, and rapidly became the clinician's number one choice as an Emergency Ventilator for the treatment of COVID-19 patients in an expanded intensive care setting.
To work most efficiently two separate programmes were set up. Ford took the project management lead on the Penlon programme and Smiths established contracts with GKN Aerospace and Rolls-Royce to help deliver their programme.
Penlon was making only 12 devices a week and the scale of the challenge to produce 2,500 a week required a massive multi-business undertaking. A new Penlon consortium was formed as the delivery mechanism and our story follows this in more detail.
Going from years and months to hours and days
To get access to the design drawings and intellectual property from Penlon, and to enable open collaboration, Non-Disclosure Agreements (NDAs) had to be signed by all parties. This could have taken weeks in normal circumstances, but all NDAs were signed in a matter of hours. This allowed the teams to start to get down to the details and understand the true scale of the challenge.
Within days, the teams had started to analyse the designs and parts list. The scale of the programme presented a range of complex and time sensitive issues including standing up a supply chain and a complex logistics network at a time when countries were starting to lock down borders and access to suppliers was becoming increasingly difficult. It was also clear that the massive challenge to build thousands of ventilators in a matter of weeks would not be possible in the existing manufacturing facilities at Penlon and further sites would need to be set up.
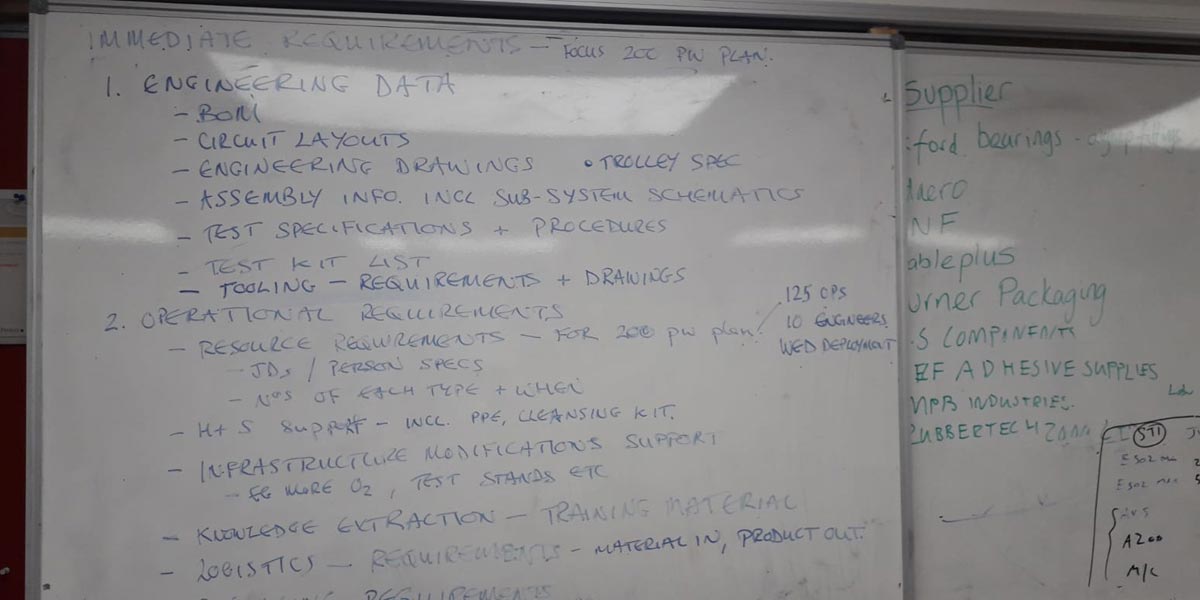
All this was possible because everyone had the same core mission and were driven by the same goal - to help supply our NHS. When done collaboratively, there was a shared sense of achievement for every milestone reached. Bringing so many organisations and people together brings its own challenges.
Securing regulatory approval
Adherence to the medical regulatory requirements was a fundamental part of this programme. The Penlon ESO 2 is an intricate and highly complex piece of equipment with 700 parts. Any medical device in the UK needs to be approved for use by an accredited notified body. However, in this crisis situation, a special dispensation can be requested for emergency devices such as the Penlon ESO 2, which then has to be approved for use by the UK Competent Authority Medicines and Healthcare Products Regulatory Agency (MHRA).
The Penlon ESO 2 achieved full approval three weeks after the consortium pitched the idea to the government, NHS and MHRA.
To put that into context, approvals normally take up to 270 days.
Building a supply chain for a complex system
Over 15 million parts were acquired from 88 suppliers worldwide in four weeks through a complex logistics network. Many parts had two, three, four or even five suppliers out of necessity to meet the rate required and to ensure there was always a back-up plan.
McLaren managed the supply chain, deploying engineering, project management, purchasing, logistics and manufacturing teams. They worked with around 100 suppliers and deployed their own machine shop and inspection capacity to support the work whilst coordinating input from other UK-based Formula 1 teams. McLaren itself produced over 70,000 complex parts with zero defects in five weeks to fill gaps in the supply chain.
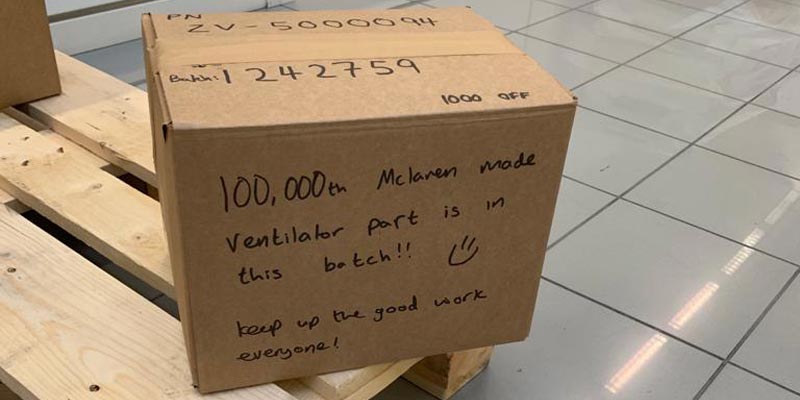
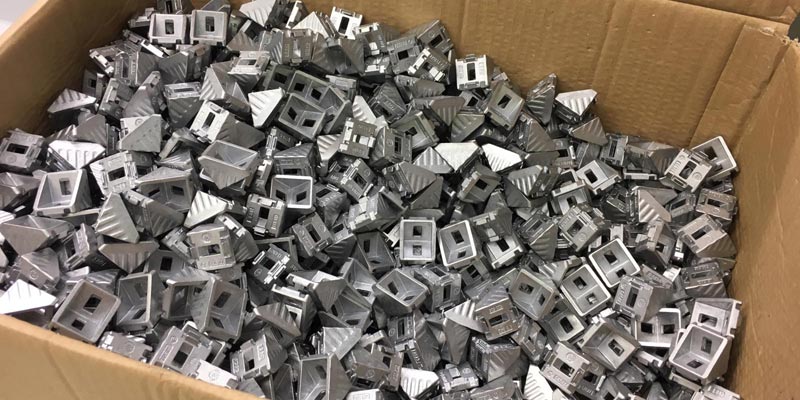
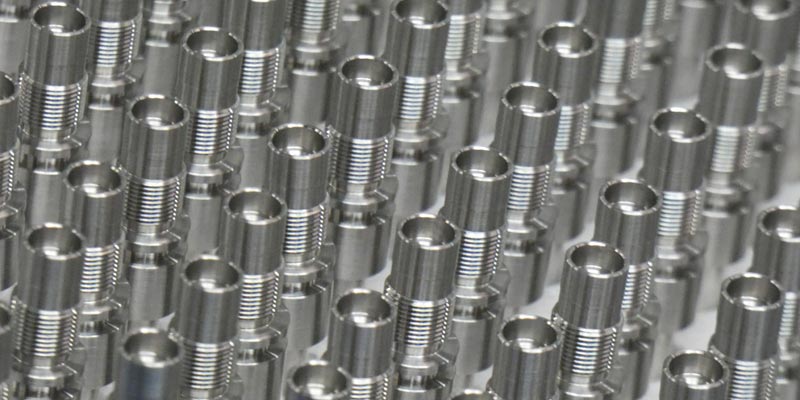
Microsoft Dynamics 365
Microsoft Dynamics 365 Supply Chain Management including Procure 2 Pay was launched for the consortium in three weeks, instead of the usual 12 months. This enabled them to order parts and oversee the whole process through to the manufacture and assembly of the finished product, allowing them to respond to changing needs quickly and effectively. Power BI was also used to give the consortium information reports including work in progress, supply chain, and logistics.
Microsoft's technology has been a significant tool in making a project of this size simple to handle and manage.
Built to support now and in the future
Penlon maintains an accredited Quality Management Systems and, in partnership with Siemens Healthineers and others, was able to bring over 100 new suppliers into its approved supply chain through desk top assessments, audits, and site visits. A huge effort was also needed to qualify the partnering sites of Airbus, McLaren, Ford, STI, and DHL with all facilities and processes needing auditing before production ramp up could commence.
The joint quality teams worked very closely together in the delivery of training, alignment of production processes, inspection, documentation, digital aids, supplier quality, and the legality of the device history records that accompany every Penlon ESO 2 ventilator; ensuring a single voice to assist in the quality message and drive consistency.
After 190 document submissions, opening test laboratories that were closed, stretching their technical and regulatory competencies, together with an immense level of technical scrutiny by MHRA and notified body; Penlon received its internationally recognised CE Certificate. It is believed that this is the first time a product that changed its intended use (from anaesthesia device to ventilator) has achieved a CE marking and is the quickest that one has been achieved. This permits the Penlon ESO 2 ventilators to continue in service post-COVID-19 for the expected lifetime of the device.
How do you train 3,500 people?
Not only did the teams involved have a significant knowledge gap to overcome to assemble these lifesaving devices, but they faced the added complexity of recruiting and training over 3,500 people under new and challenging workplace guidelines set by the government.
The knowledge, understanding and years of experience gained by Penlon in manufacturing these devices had to be passed on to all the operators who build, calibrate, and test the ventilator control systems with the same degree of quality and consistency. This required compressing the timeline for the selection, training, and deployment of operators from what would normally take several months to a few days. At Ford alone, the sub-assembly plant inducted over 850 people and completed over 18,000 hours of training (that's over two years of training) in seven weeks.
Microsoft HoloLens 2
How do you train 3,500 people? By using Microsoft HoloLens 2 and mixed reality. Balancing the twin imperatives of speed of delivery with the absolute adherence to regulatory standards that is needed to ensure patient safety, the HoloLens 2 were used to train the teams quickly and safely without close-contact assistance. This allowed expertise from Penlon to be shared with sites up and down the country as they worked to assemble, and test ventilators for the first time.
Not only did it accelerate training, but it allowed employees to get help and guidance by connecting with remotely located technical experts. This minimised unnecessary travel and the risk of social contact, particularly as several technical specialists were required to shield at home.
100 HoloLens 2s were configured to help train and remote assist technicians building ventilator parts.
Microsoft's mixed reality headset has been used to capture the highly specialised ventilator production process to train and upskill the consortium's new workforce in multiple manufacturing sites across the UK - many of whom have been brought in overnight and are used to manufacturing aerospace and automobile parts. A step by step guide has been added to training footage captured on HoloLens 2 for workers to use across the country as they build replica assembly lines from scratch and begin production.
Unifying across the country
Once the supply chain was created, the Penlon ESO 2 was broken down into four sub-assemblies that were scaled up at various sites across the country before being brought back together into a final assembly.
Airbus was responsible for producing and assembling the absorber and flow meter sub-assemblies of the Penlon ESO 2 ventilator.
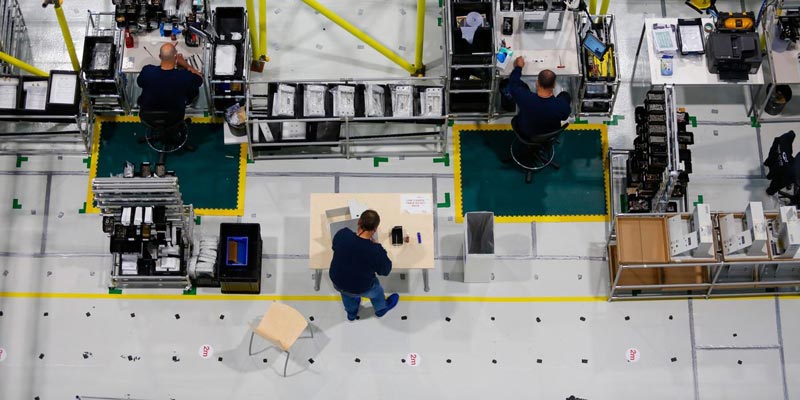
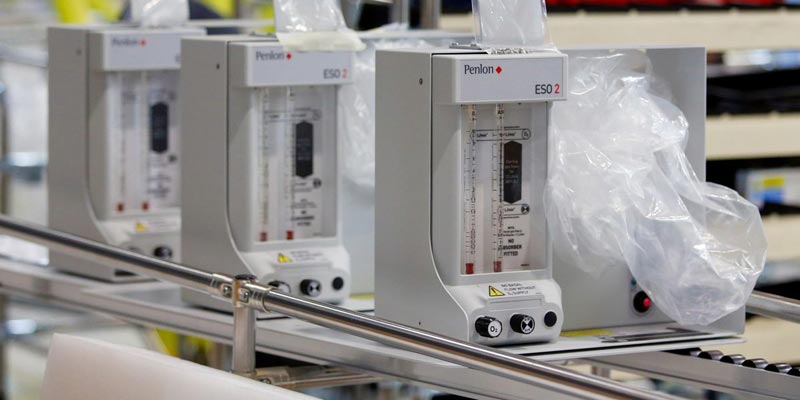
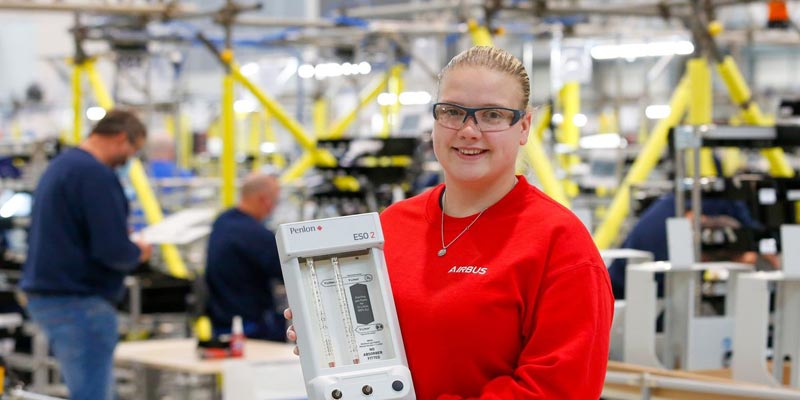
Working with Siemens, they used a digital twin approach to design the new Production Systems remotely without sight of the physical product or plan. Manufacturing lines were designed, validated, and delivered within three weeks. Normally, this takes between 12 months to three years.
550 Airbus employees worked across shifts to enable round the clock working, some changing their day to day activities from repairing and inspecting aircraft in Singapore to building ventilators for the NHS in north Wales.
Even the local community got involved, with hardware stores staying open late for the teams to pick up basic tools, to engineering firms coming in on a weekend to support.
At the Ford factory, over 10,000 hours of manufacturing engineering in two weeks allowed them to transform a building at their Dagenham Engine Plant into a sub-assembly production site manufacturing the AVS vent box and remote display screen for the Penlon ESO 2.
650 Ford employees worked together across 190 individual workstations in a social distanced production line over three shifts a day, before sending the sub-assemblies to STI.
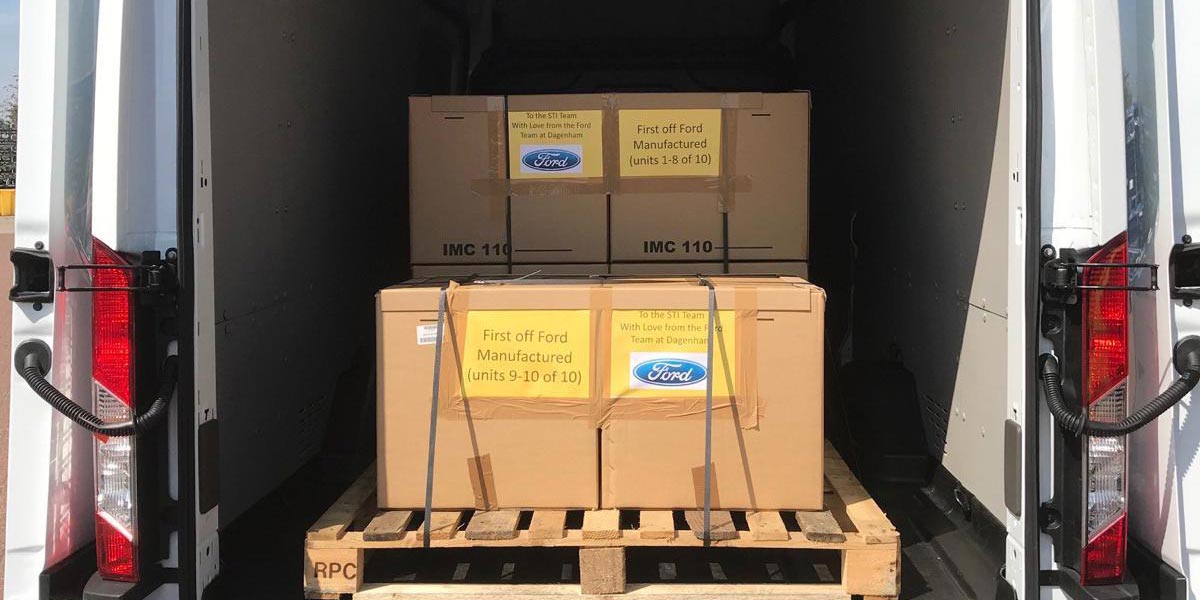
McLaren transformed their trophy and F1 car-filled factory into a facility to design and produce bespoke trolleys on which the ventilators are fixed, and which are suitable for use in clinical settings.
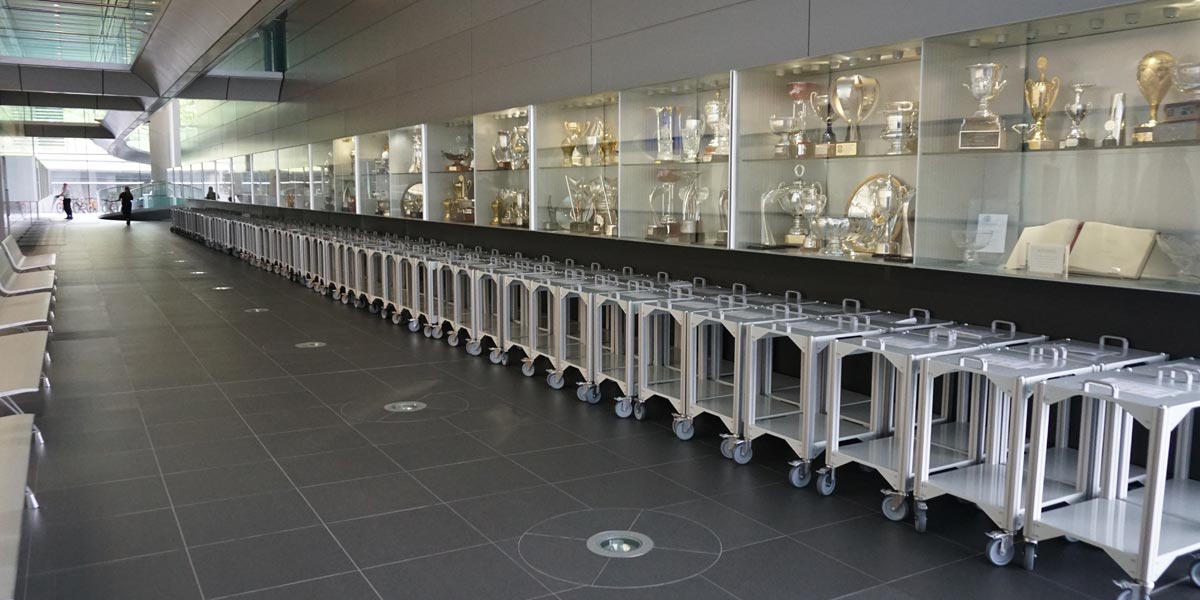
They used their design and engineering expertise in lightweight, user-friendly design to develop a solution that was quickly scaled to allow them to produce 250 trolleys a day.
The trolley, AVS vent box, absorber, and flow meter sub-assemblies from McLaren, Ford, and Airbus are then sent to Surface Technology International (STI) where 130 specially trained staff assembled the parts into the final product. To facilitate this project STI took on and trained 70 additional staff, including friends and family of STI employees as well as people from the local area.
A ventilator is completed every 88 seconds.
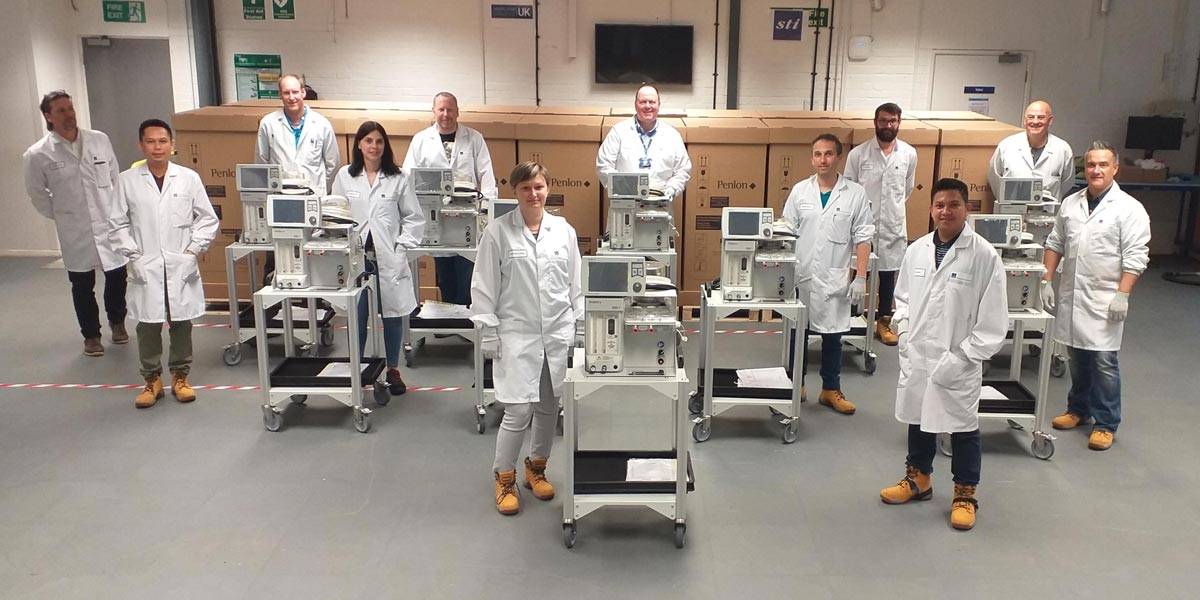
The final ventilator then went to Penlon. Previously, they would produce the whole ventilator but here, their role became to perform final testing and product release. The whole Abingdon factory, as well as a second site of 60 people at GKN Automotive, was converted into final test stations.
Penlon went from 55 people working in production to 550 people, including the UK F1 teams, working over six shifts. Once approved, the ventilators were then shipped on to the NHS to help them treat patients.
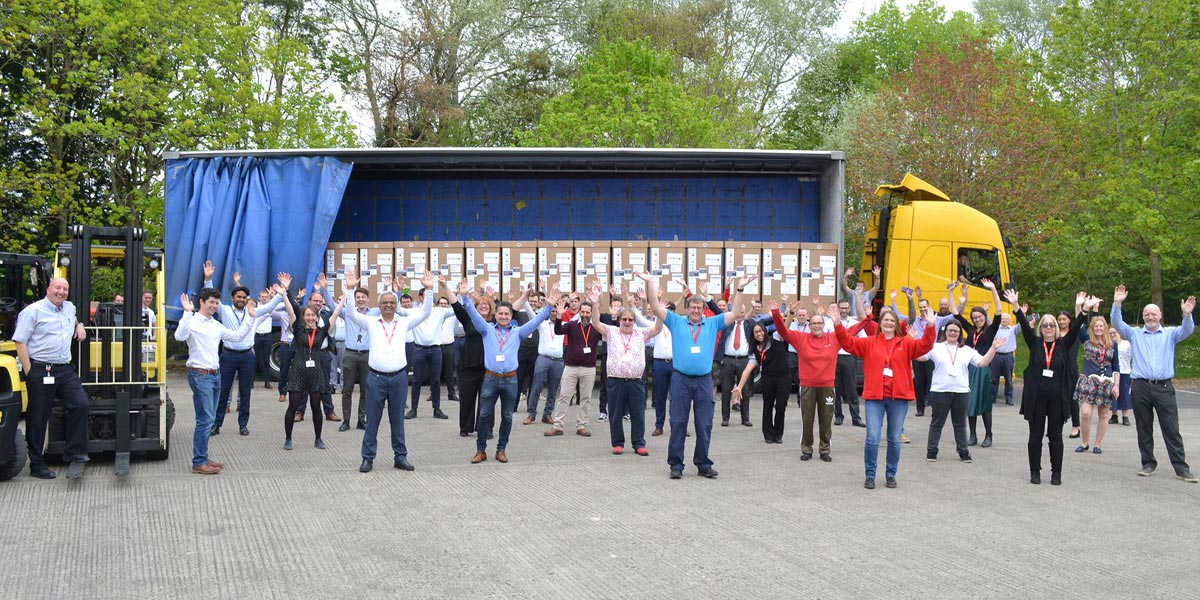
Penlon's range of medical device equipment, which they normally export 95 percent of, was all put to one side so that they could focus exclusively on the Penlon ESO 2 for the NHS.
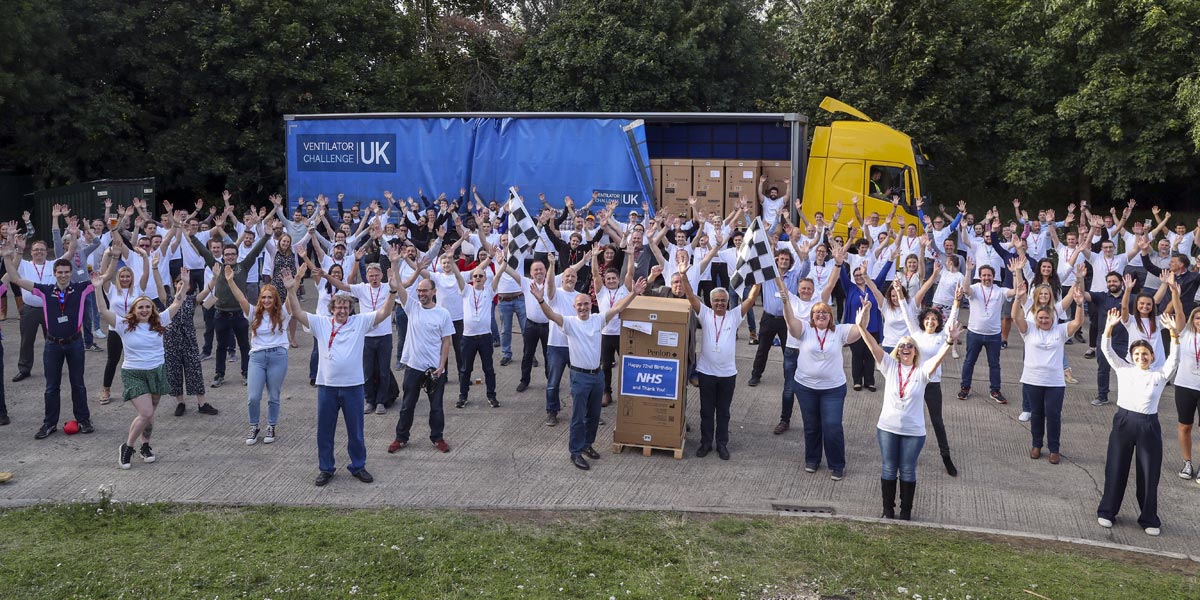
Continued support for the NHS
Once a ventilator reaches the NHS, it doesn't just stop there. Inspiration Healthcare expanded their 24/7 service to include all ventilators produced by the consortium. Trained by experts at Penlon, they were able to provide bedside support for doctors and nurses needing guidance on the machines when in use on critical care patients.
What happens when we unite
Building thousands of ventilators was a compelling purpose that intrinsically appealed to each consortium member. This was a challenge beyond what they had done before - and there was no book on this.
This powerful motive pushed a team who self-organised around the task. People were picked for their skills and passions, with a flat workstream structure. There were no badges or hierarchy - results always trumped stripes and the team worked cohesively.
Decisions were made at the point of greatest knowledge, using openly accessible data, which in turn drove agile processes. Processes and product were produced in parallel. With well managed communications and project boundaries, the team was kept autonomous.
With this built trust, everyone was empowered to go beyond a can-do attitude to a will-do attitude. The focus was on output, with the acceptance that this extraordinary circumstance meant that the normal 9-5 workday wouldn't work. This inspirational culture spread to every corner of the consortium driving a deep common bond between people, many who had not actually met each other.
Ventilator Challenge UK just proves that when humans come together, they can solve a problem - no matter the risk. When you combine trust, openness, selfless teamwork, with inspiring people, and the great British 'will-do' attitude, you can achieve the impossible.
The acceleration of production was exponential as teams gained knowledge and solved issues. The first 100 devices took four weeks to build, the final 1,000 took 2.4 days. By the end of the programme, production was ~150 times quicker than previously achieved in Penlon. Penlon would ordinarily have been producing about 50 ventilators per month.
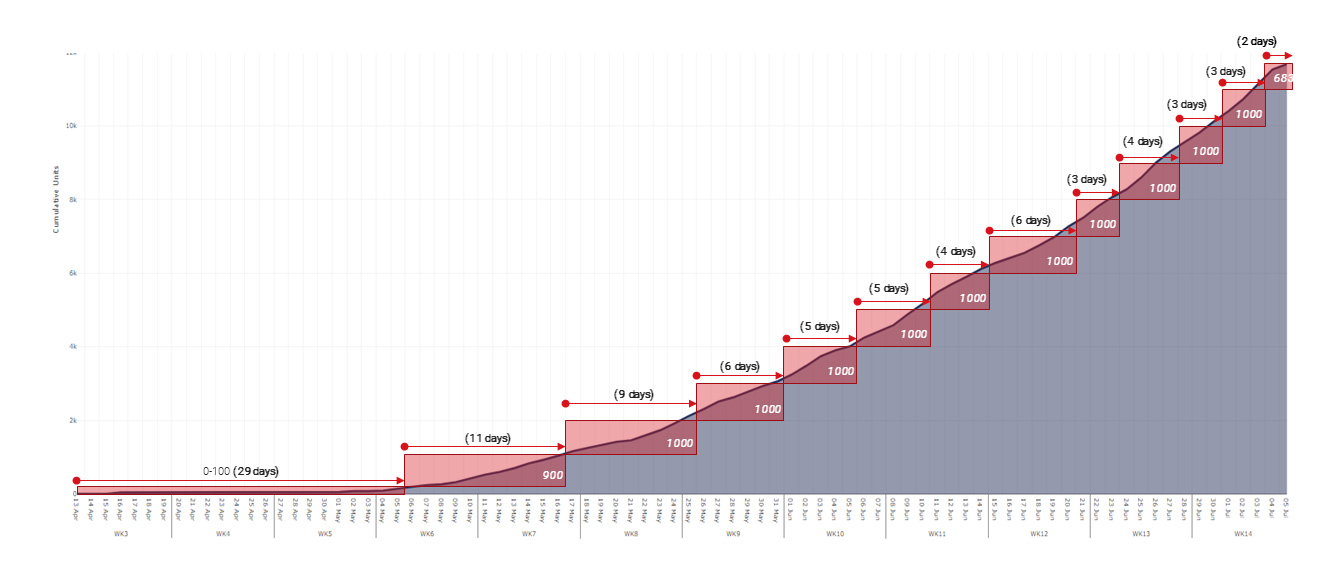
The consortium produced a total of 13,437 ventilators in this period.
Ensuring the NHS has enough ventilators to treat patients with advanced COVID-19 symptoms has been critical to the UK's continued battle against the disease. Microsoft and its partners have been instrumental in providing the tools that have enabled the Ventilator Challenge UK consortium members to collaborate effectively, manage complex supply chains and train staff in new manufacturing procedures. In doing so, we've been able to gear up to manufacture 20 years' worth of ventilators in just 12 weeks.
Originally published on 08/07/2020 / © Microsoft
Consortium members
Discover how some of our Ventilator Challenge UK consortium members and suppliers contributed to the challenge.
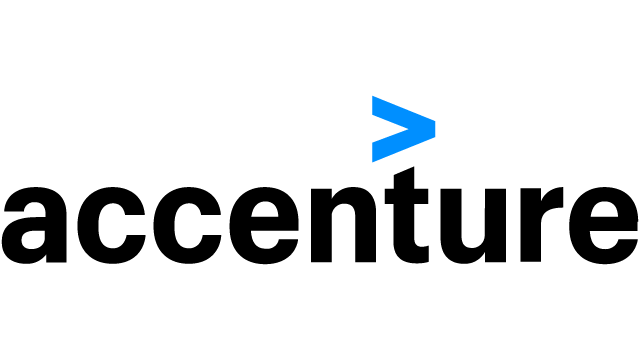
Accenture worked with Rolls-Royce to design, manage and operate the supply chain for the Smiths programme, orchestrating the purchase and shipment of 3.4 million parts from more than 100 suppliers to three manufacturing locations for assembly.
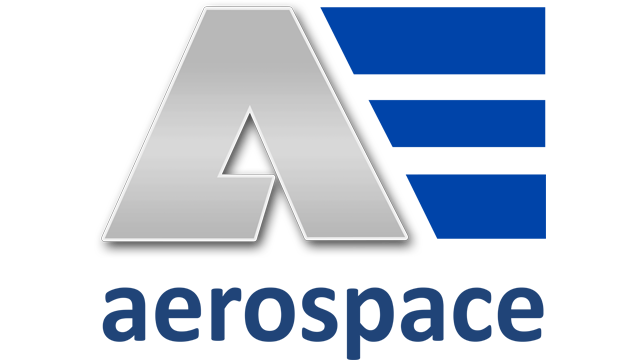
On the afternoon of Friday, the 27th March, Rolls Royce Control Systems asked AE Aerospace if they could machine a number of prototype parts over the weekend and produce, in volume, a part for the Smiths paraPAC plus™ ventilator. From the 27th, they worked through to early Monday morning on the 30th to successfully produce the prototype parts. Over the following 2 weeks, they moved most of their machines onto the Ventilator Challenge project and worked 24/7 and involved almost everyone in the facility. They completed the production run on Good Friday. During this time, one of their team, Mark Niblett, became ill with COVID-19 and was admitted to hospital and placed on a ventilator. Sadly, Mark did not recover and passed away on the 23rd April. AE Aerospace have dedicated this work to him.
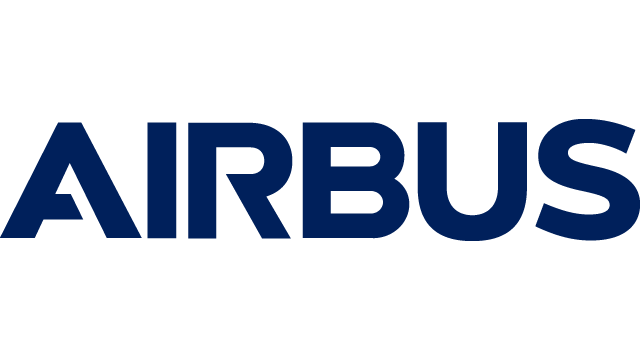
Airbus and Siemens rapidly transformed AMRC Cymru in Broughton, North Wales, from a research and development facility into an assembly line to produce ventilators within 24 days of being tasked by the Ventilator Challenge UK consortium. Siemens fast-tracked the design, validation and delivery of the assembly lines using a digital twin approach allowing Airbus to quickly deploy over 550 employees across 16 assembly lines. The AMRC teams are working 24 hours a day, seven days per week, in five teams of 'four on, six off' shift patterns, to produce absorber units and flowmeters for the Penlon ESO 2 Prima ventilator. Training of the teams started on 6 April with full production starting on 13 April.
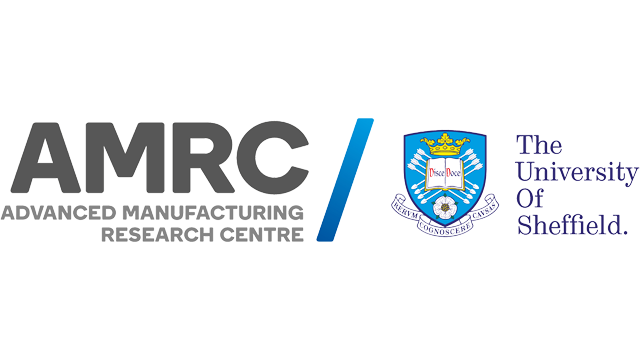
The University of Sheffield Advanced Manufacturing Centre (AMRC) assisted with the collection, configuration, and deployment of Microsoft HoloLens 2 AR devices for the Ventilator Challenge. Manufacturers used these devices to train workers in ventilator assembly, to approve workers as being suitably trained, and to provide real-time support from remote experts to the manufacturing sites around the country. Over a weekend, the AMRC machined a family of ventilator parts to help prove out the ventilator assembly process before the production parts arrived. In mid-March, AMRC Cymru become part of the Ventilator Challenge UK by providing the facility and resources to manufacture the absorber and flow meter modules for the Penlon ventilator. A joint team was immediately put together to convert the building so that it would be a COVID-19 safe environment for the manufacturing team to operate. Over the course of 3 weeks, using digital tools such as Discrete Event simulation, they were able to achieve this and hand over to Airbus Operations to run the manufacturing operation.
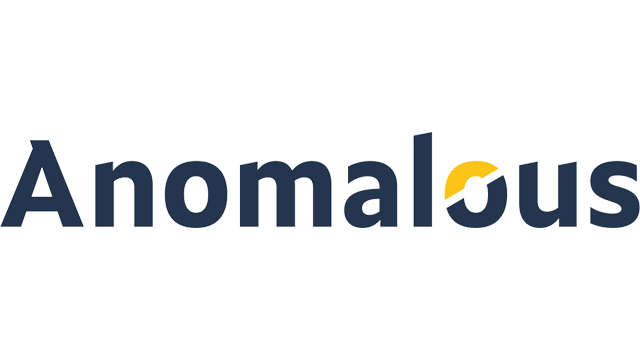
Anomalous used their data platform and AI-based inspection technology to develop a mobile application that was able to recognise ventilator parts to aid operators in visually identifying parts during assembly and inspection.

Arrow Electronics serves as a supply chain partner for the UK Ventilator initiative. In this central role, Arrow managed the global electronics supply chain to provide Penlon with the processors, sensors, printed circuit boards, and other components needed to precisely operate and monitor the ventilator's key lifesaving functions. This started with engineers analysing the ventilator's updated and simplified design for coronavirus treatment and aligning it to Arrow's global network of electronics suppliers and inventory. Arrow secured more than 30 million components for the ventilators. In some cases, Arrow businesses sourced scarce and high-demand parts, as well as identified alternative products to meet the initiative's accelerated schedule and stringent requirements. Then, asset managers secured the components and transportation managers shipped components through a network of warehouses and ports to technology manufacturing and assembly locations in the UK - services that Arrow helped to arrange in a matter of weeks. Arrow's central role in the ventilators' development and production was facilitated by its existing relationships with other aerospace, automotive and medical companies in the consortium, including McLaren.
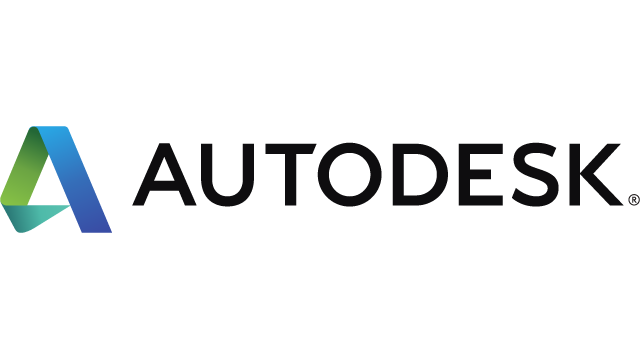
Autodesk supported the Ventilator Challenge UK consortium through several initiatives designed to assist consortium members. This included providing design and manufacturing advice to consortium members via their team of design, manufacturing, and process specialists on any aspect of ventilator and/or PPE design and production. The company also connected members to additional suppliers to build the agile, scalable supply chain, such as specialist expertise or additional production capacity. Support was also provided through cloud-based design and manufacturing tools, to help optimise the design of ventilators and production time, and collaborate faster and more effectively remotely. Lastly, the Autodesk Technology Centre, Birmingham, operated on a limited basis to support efforts with the development and testing of prototypes via the technologies and resources available in the facility.
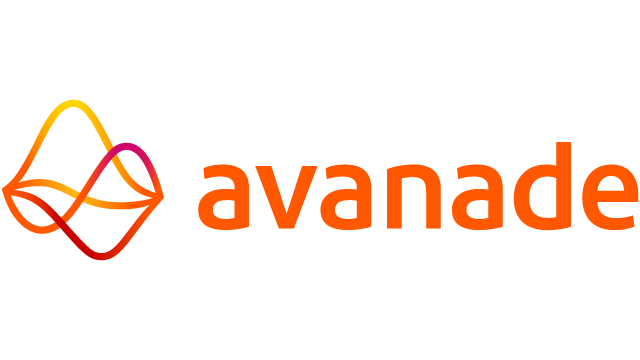
Leveraging Microsoft Teams, Dynamics 365 Supply Chain Management, Dynamics 365 Remote Assist, HoloLens 2, Power BI and the Azure cloud platform, Avanade supported the challenge through 1. Ventilator Assembly Line Training via Mixed Reality - Avanade digitized both Smiths' and Penlon's ventilator CAD drawings and assembly guides for HoloLens 2 devices, enabling a mixed reality experience for assembly line staff from various consortium members. Avanade delivered an associated Mobile Device Management service, providing an 'over-the-shoulder' remote expert solution linking Smiths and Penlon experts with assembly staff, 100s of miles away, which is a key pillar for success. 2 Rapid Supply Chain Enabling all consortium members to operate as one team - Microsoft Dynamics 365 was used to enable the consortium to order parts and oversee the process through to payment. In just three weeks, Microsoft, Avanade, and Accenture, created a new supply chain solution that enabled inventory components to be procured, tracked, receipted, and paid for. Avanade leveraged its Intelligent Enterprise Solutions, Industry best practice, standard solution functionality and a collaborative, smart and agile team culture.3. Control Tower Dashboard giving output visibility - the supply chain in the Ventilator Challenge UK consortium asked Avanade to build a 'control tower' dashboard to provide the many different companies a single source of truth of analytics for the production of the ventilators. From visibility to the supply chain of the Smith's Ventilator components through to sub-assemblies and testing and on to final delivery at the government holding site, Avanade provided a 360° live view of production, made available to all stakeholders 24/7.
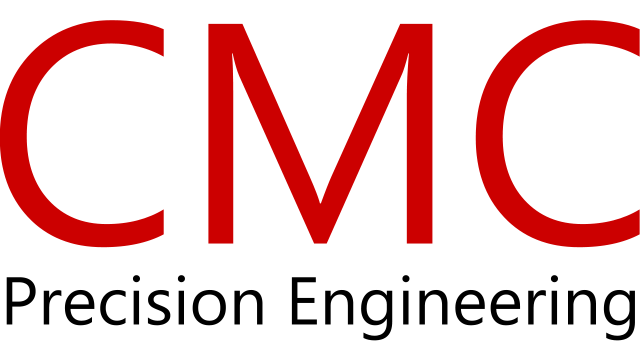
CMC have been working to produce CNC turned and milled precision parts for both the actual ventilators and the ventilator test equipment. Our hard working and skilled engineers have enabled us to produce the required components in a short timescale without compromising on quality. It has been a pleasure to be part of such a critical project.
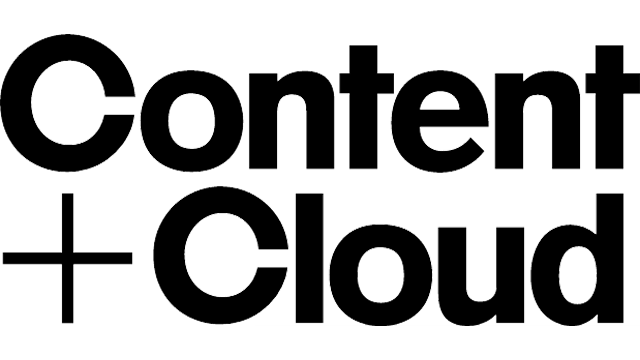
IT Lab, now Content+Cloud, provided a dedicated identity, authentication, and application service desk to enable and support productive, secure collaboration and communication amongst consortium members using Microsoft 365 and Teams.
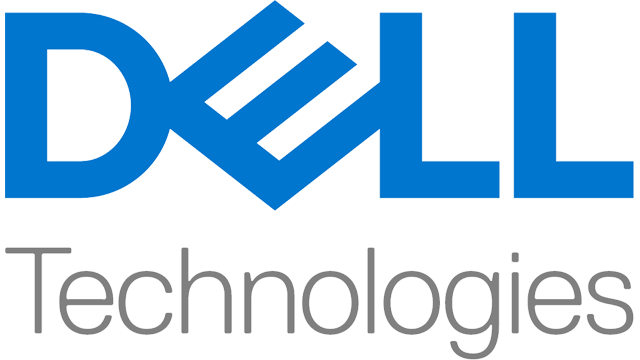
In partnership with McLaren, Dell Technologies provided consultancy to the consortium and supported remote working and production line monitoring for Penlon’s supply chain and production staff. Assembly site equipment included conferencing equipment, Dell OptiPlex workstations and a large Dell 75-inch 4K Interactive Touch Monitor for production line monitoring. Latitude 7400 laptops enable remote working and Penlon team members use Latitude 7540 laptops for data-intensive tasks.
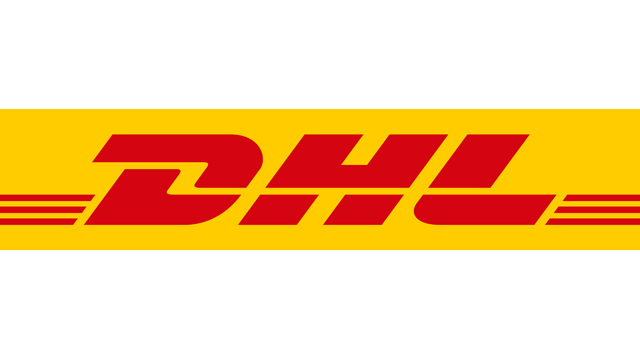
DHL designed a new supply chain to support in just 1.5 weeks with 120 team members involved, a complete installation of an IT system and 700 racking locations created all in a Social Distancing environment. DHL made 2,031 Supplier Collections from 196 different suppliers, picking up 8,423 pallets and cartons of ventilator parts. 97% of the collections were same day and the team have achieved amazing collection-on-time performance of 99.2% within a 2-hour window. DHL made 220 critical deliveries of parts into ventilator manufacturers for assembly (Ford, Rolls-Royce, GKN, Airbus, McLaren) and had 3 football fields of warehousing space, at Stirling Park, Fradley Park, and Tyrefort. In total, DHL picked and shipped over 6 million components equating to 40,000 cases delivered and over 17,000 forklift truck miles.
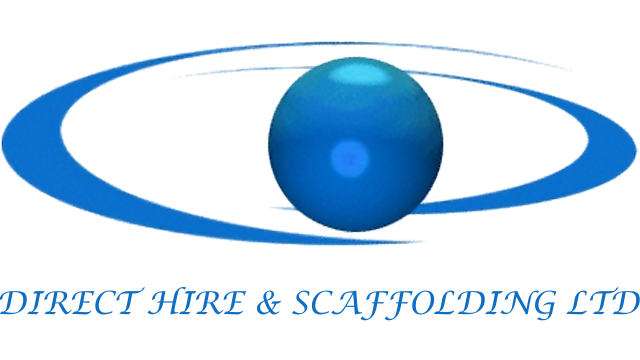
Direct Hire & Scaffolding were approached by their longstanding customer, Ford, to work on the project, and were very keen to be involved and provide any necessary assistance and advice. This was a new and urgent facility that needed to be operating within a short period of time. There were some initial challenges to overcome due to the project's unique and unfamiliar format. Building a temporary conveyor line specific for ventilator production necessitated careful planning due to the new COVID-19 guidelines. This included sequencing works with other construction workers whilst socially distancing. The layout and specification of the project was provided by Ford Motor Company under the guidance and support of Hamton Environmental Services. The clear goal for all involved was to work collaboratively thus ensuring finalisation of the project which ultimately saved lives in this crisis.
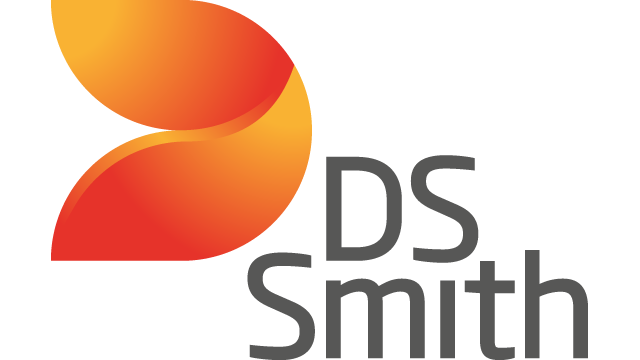
DS Smith, the leading provider of sustainable paper-based packaging solutions, was selected as the provider of choice to deliver packaging for the safe transit of the first government approved ventilator which is being produced by the Ventilator Challenge UK consortium. This time sensitive project involved a number of different materials including three different sized boxes, labels, strapping kits, and pallets as well as the co-ordinated production from multiple sites.
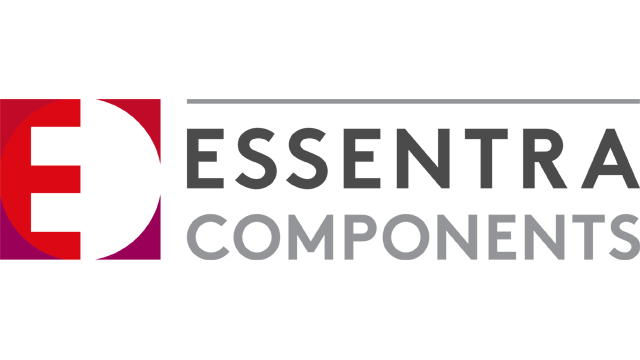
Essentra Components, a UK based manufacturer with an established supply chain and extensive production/supply expertise, supported Penlon with a variety of components for the manufacture of the Penlon ESO 2 Emergency Ventilators. Explained Scott Fawcett, Managing Director "Our team here at Essentra Components are proud to be supporting the medical industry in general including the Ventilator Challenge UK, and Penlon in particular - we were delighted that our account manager was able to personally organise delivery at speed, at scale to this crucial customer." Andrew Wright (Senior Buyer) and Mike Barlow (Purchase Director) were grateful for the immediate response, "Thanks so much for arranging to get the 60,000 parts to us today - we really appreciate it. This means that we can complete the first 30 ventilators for the NHS and get them out to them tomorrow. We can't ask for more.

Ford played a significant part in a distributed manufacturing system supported by all the consortium members. Their contribution included overall project leadership for the accelerated Penlon scale up manufacturing project; manufacturing and testing of the ventilator sub-assembly unit at Dagenham; manufacturing planning, procurement support and involvement in supply chain logistics; and assisting with Manufacturing Engineering for Airbus, Penlon and STI locations. Employees worked for three weeks to turn an unused warehouse on the Ford Dagenham Estate into an ISO9001 accredited high-tech operation. Existing equipment was repurposed and quickly established a production line for components boxes and 8.4-inch remote display screens that form key parts of the fully assembled units.3D printing processes were employed to make key components for 200 socially-distanced workstations for the Ford volunteers that include operators, product coaches, technicians and engineers. At full production, more than 650 people worked in three shifts at the facility. To collaborate day-to-day with Penlon, the Ford team uses HoloLens 2 mixed reality headsets, enabling remote technicians and specialists to view the perspective of the HoloLens wearer on a computer screen and provide real-time guidance and information, seen as holograms in the wearer's field of view.
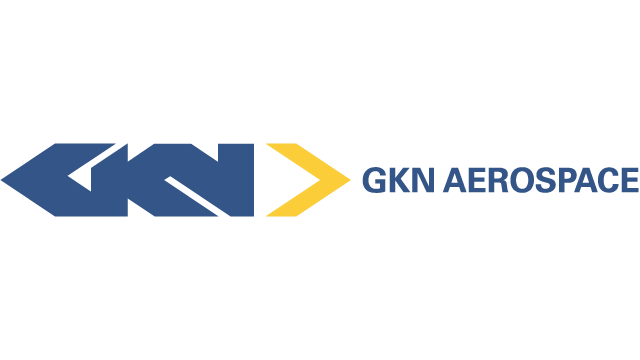
GKN's initial role was to capture requirements from HMG and help the wider consortium, and Smiths specifically, to create an effective team of companies to achieve the significant industrial scale-up required. After moving to the delivery phase of project, GKN was specifically establishing additional production lines to scale-up the manufacture of Smiths paraPAC plus™ ventilator. They used their facility in Luton (15 minutes from Smiths' site) to define a production flow line capable of being scaled up to meet the volume requirements. Once the Luton line was established and proven, GKN replicated one production line on the Isle of Wight and in parallel enabled Rolls-Royce to add additional assembly lines at Filton.
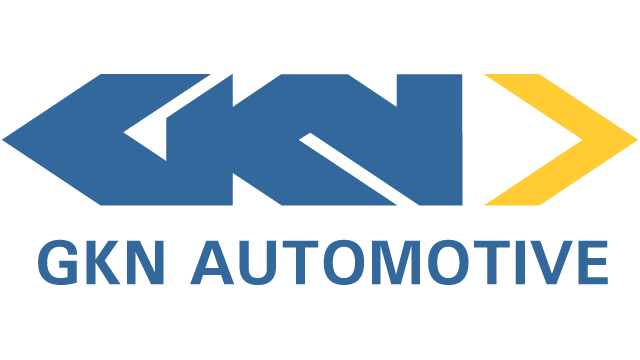
GKN Automotive's Innovation Centre supported Penlon with more Final Machine Testing (FMT) capacity for its ventilator and helped accelerate production of the Penlon ES02. The facility also had the added advantage of being just across the road from Penlon. In less than three weeks the GKN Automotive Innovation Centre repurposed its facility to accommodate an additional 15 testing stations, dedicating over half its team to the project.
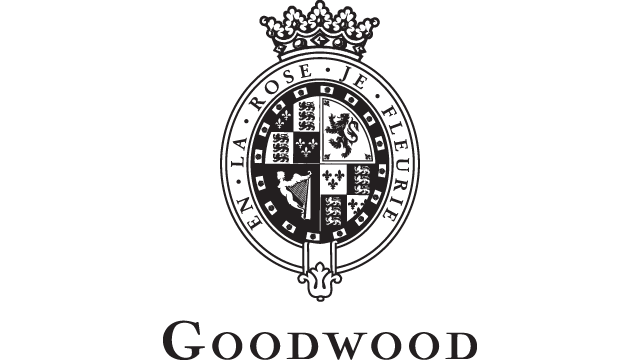
Goodwood has been home to horseracing since 1801 and the racecourse is loved by many for its sweeping views of the South Downs and Sussex coastline. The racecourse usually welcomes thousands of racegoers, who come throughout the season to enjoy a day out on the South Downs. However, this year, due to the pandemic, racing is only able to take place 'behind closed doors' and all the hospitality areas are empty. The Duke of Richmond was pleased to be able to open up these areas in order to store medical trolleys which, along with other vital equipment required for ventilators, were used in both existing and Nightingale hospitals to support patients with severe COVID-19 symptoms. This is just one of many local efforts that Goodwood has been involved in to support the health service.
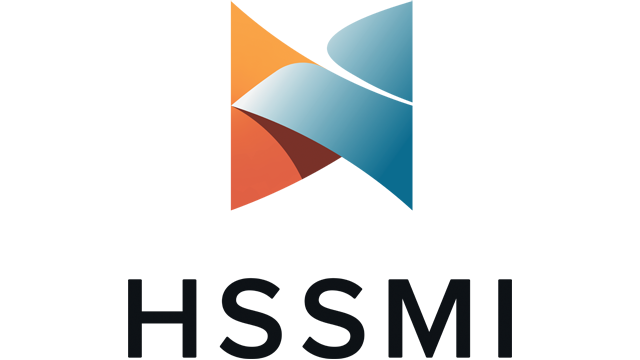
HSSMI supported Ford Motor Company to accelerate the scale up of ventilator production through help with the planning of production and the training of operators using digital tools. By developing a series of 3D, digitally animated work instructions using 3D PDF technology, HSSMI enabled operators to be trained remotely under the constraints of social distancing. Firstly, by scanning the factory of an incumbent ventilator manufacturing facility and assembly line using 360 video technology to capture the physical environment, HSSMI created an interactive digital representation. This also included information on production practices, bill of processes, facility spatial requirements, and cycle times, thus establishing a benchmark for ventilator production. Secondly, using the available data, HSSMI generated digital build instructions in the form of 3D PDFs for each operation. The 3D PDFs were easily shared and provided clear instructions and an immersive learning experience for manual operators before they safely started working on the production line. As such, scale up to full capacity was achieved more expediently, economically, and safely through the application of digital tools.
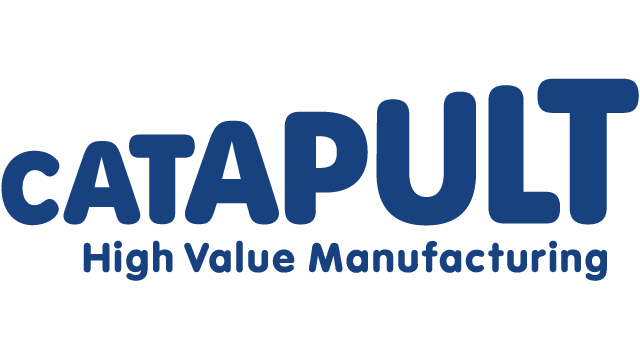
The HVM Catapult used its trusted relationships across the UK's engineering community to identify companies with both the capabilities needed and desire to help super-scale ventilator production in the UK. Following a call with hundreds of manufacturers in which the UK government formally announced its 'Ventilator Challenge', the HVM Catapult CEO, Dick Elsy saw an opportunity to help bring people together. Phoning round key contacts he quickly assembled a core of like-minded and engaged people and brought together a team with the right blend of expertise which became the founding members of the Consortium. These founding members asked Dick to stay on to chair the consortium. Many of Dick's team dedicated their whole time to the programme, with Tamarin Adshead as the driving force behind the effective operation of the executive team and Rosa Wilkinson leading the communications process across the consortium so effectively and professionally. Our Chief Technology Officer Sam Turner played a key role as the consortium started to take shape, including supporting and coordinating the development of prototypes and marshalling the broader resources of the HVM Catapult. As the HVM Catapult receives public funding we felt it our duty to offer all of our support pro-bono to VCUK. The Catapult will also make sure that lessons learned through the Consortium's work are shared across the UK's manufacturing sector.
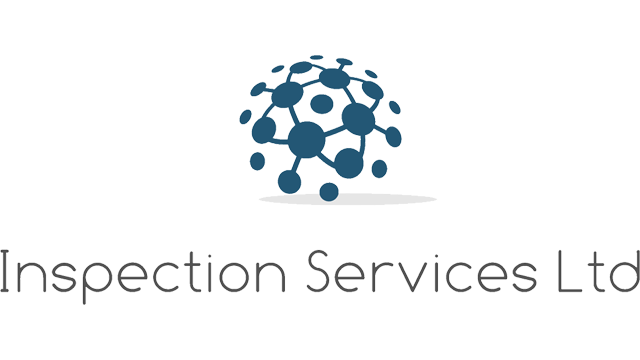
Inspection Services Ltd were invited to support the Ventilator Challenge UK project in March and were able to quickly establish teams to support the inspection of incoming stock that was to be used in sub-assemblies for the end product. By using their cloud-based reporting systems they were quickly able to report and respond back to the project in real time. By using collaborative technology, the adjustments were able to be made in the manufacturing process which accelerated production.
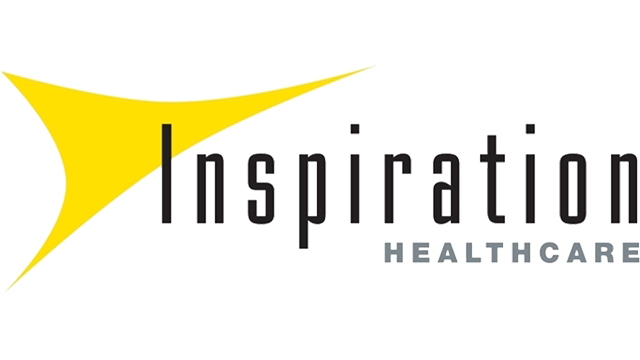
Inspiration are a 'Med-Tech' AIM Listed SME primarily providing Critical Care products for Neonatal Intensive Care as well as novel ventilation systems (some of which were used during Swine Flu). Inspiration were uniquely positioned to be able to offer advice to the consortium on the deployment and use of novel ventilators and their associated issues. They also supported the quality requirements through provision of staff as appropriate through Siemens. Inspiration understands end-user needs and delivered ventilator support to doctors and nurses by the bedside through Inspiration's own 24/7 support service.
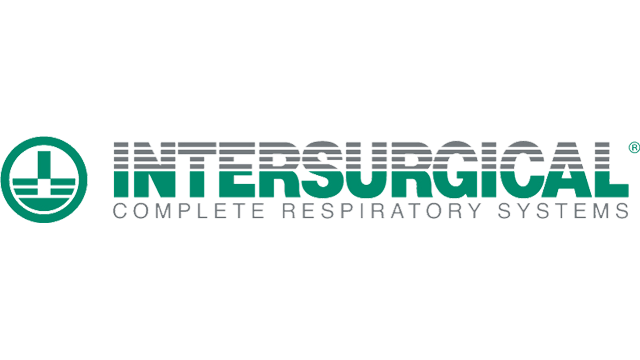
Intersurgical manufacture respiratory care consumables - including breathing systems, patient interfaces, filters, and valves that connect the patient to the ventilator. At the outset they were involved across most of the consortiums that required respiratory components to support their ventilator concepts and developments. Their teams in the UK and Europe worked tirelessly to ensure these were made available to enable these rapid, and often changing, developments to progress. They continue to supply a range of respiratory products, including breathing systems, to support the ongoing treatment of COVID-19 patients.
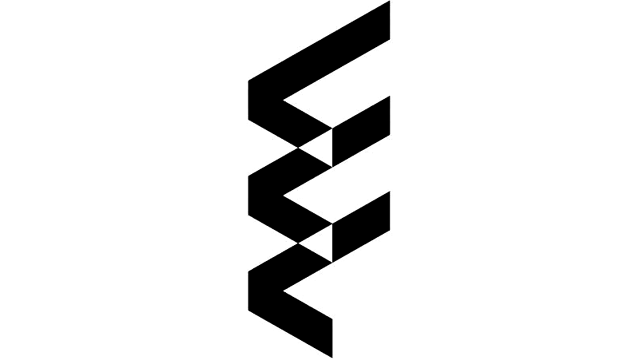
Lineside Logistics have a close and very successful working relationship with Ford Motor Company, having worked as partners for over 14 years providing on site logistics expertise ranging from material handling/sub assembly/kitting and repack solutions. Lineside Logistics were assigned to integrate synchronous material flow systems, which involved traceability in received components, material flow of individual components, packaging specifications and scan to ship of individual units. They were routinely asked to provide production line support and provided assembly labour to specific operations where greater flexibility was required in terms of rapid uplift or restriction of throughput. Their flexible operational model allowed them to provide staff to typical operations such as sub assembly processes, where their staff continue to assemble parts under strict work instructions. This model allowed them to engage over 100 members of staff to work on the Ventilator challenge.
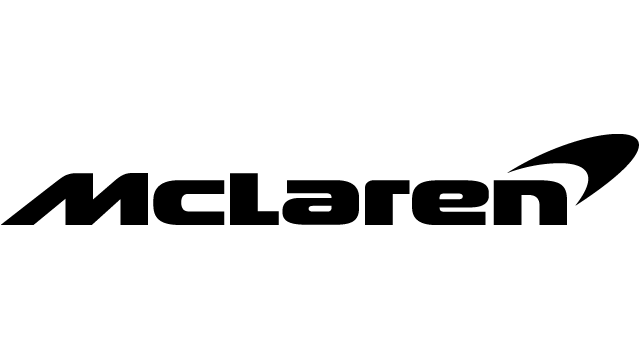
Involvement in the Ventilator Challenge UK consortium spanned the entire McLaren Group, with overall responsibility for supply chain and logistics across both Penlon and Smiths programmes, and additionally oversaw the engineering and issues management activities at Penlon. McLaren Racing deployed engineering, project management, purchasing, logistics and manufacturing teams, procuring approximately 50% of the parts to help ramp-up production of the Penlon ventilator design, handling the most complex parts and some of the most challenging supply chain aspects of the programme. McLaren Racing worked with around 100 suppliers and deployed its own machine shop and inspection capacity to support the work whilst coordinating input from other UK-based Formula 1 teams. Both Racing and Automotive teams designed bespoke trolleys on which the ventilators are fixed for use in clinical settings using its design and engineering expertise in lightweight, user-friendly design has been deployed in the trolley design. McLaren Automotive deployed engineering expertise to reverse-engineer, design, procure and build 'end of line' test equipment to ensure that the Smiths ventilator units met all of the specified functional and safety requirements. McLaren Applied deployed exceptionally skilled engineers to reverse engineer several critical electronics boards for use in the Smiths test boxes, and to support the specification of suitable replacement parts where original equipment was no longer available.
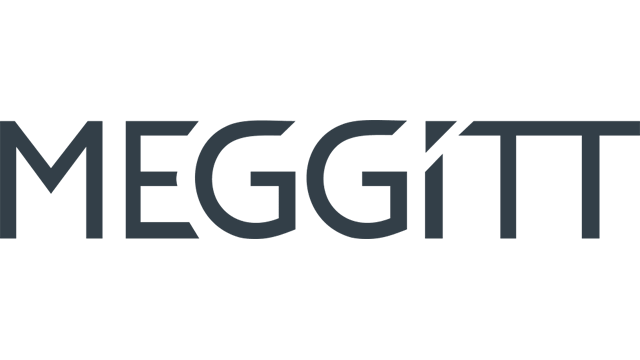
Meggitt led the Ventilator Challenge UK's Programme Management Office, supporting the Quality Assurance and Regulatory Affairs work-stream. They also led the development of the Spiritus Rapidly Manufactured Ventilator: the consortium's contingency plan, if additional intensive care ventilators were needed beyond what could be delivered from the other Ventilator OEMs.
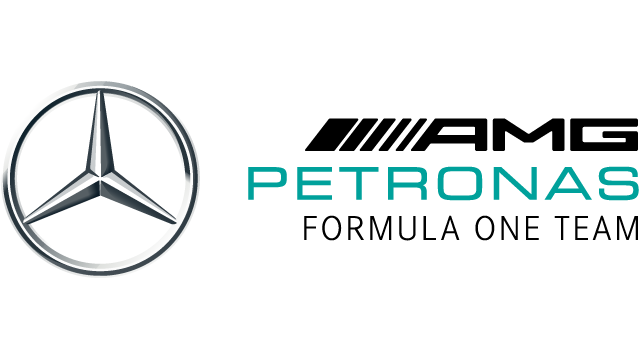
The Mercedes-AMG Petronas F1 Team has 43 volunteers from across the business working in the testing and pass-off process for the Penlon ventilators across day and night shifts in Abingdon.
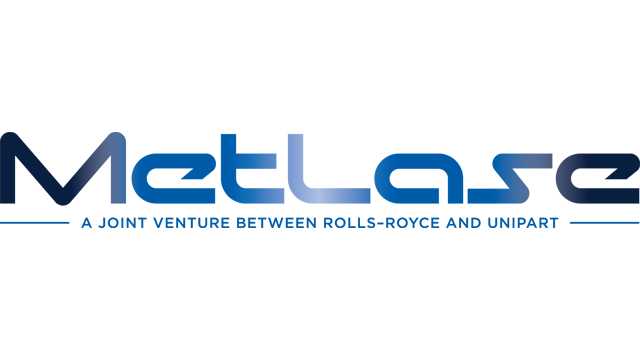
MetLase, a joint venture between Rolls-Royce and Unipart, used their unique patented methodologies, laser-cutting, press-brake forming and in-house developed digital technologies, to deliver a multi-facetted contribution to the Ventilator Challenge UK. MetLase developed their own ventilator, with design emphasis focussed on availability of components within the supply-chain and manufacturability, while remaining compliant to the MRHA's specification. The first prototype was tested within 14 days. MetLase knew that meeting the MHRA's specification would be challenging, so brought together a regulatory compliance team equal in size of their engineering team. Including MetLase's own compliance lead, and expertise from parent companies Rolls-Royce and Unipart Rail, external contributors included Sheffield Teaching Hospitals, innovation experts CPI and the public health and safety organisation NSF. Manufacturing and supply-chain activities were led by Unipart Manufacturing, who sourced components and designed production lines within their Coventry manufacturing facilities. MetLase aided other companies in the VCUK consortium: Meggitt PLC: with the design, manufacturability, and initial production runs of the enclosure for their Spiritus ventilator project. Rolls-Royce: MetLase designed and produced 72 bespoke manufacturing workstations in just 10 days, for the new production lines in their Bristol facility, to scale up production of Smiths paraPAC plus™ ventilators.
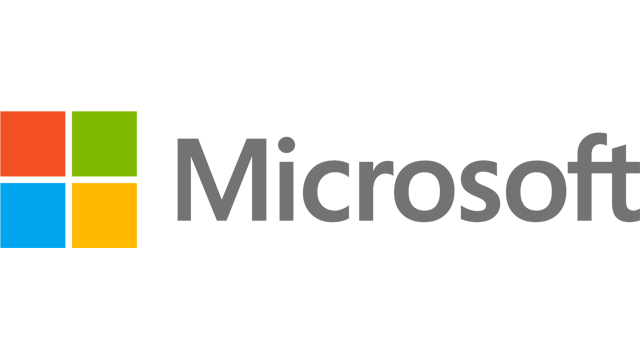
Microsoft provided technology such as Teams and Dynamics 365 to help track and support the supply chain and enable secure collaboration. The consortium was able to use the HoloLens 2 to train and assist in the building of ventilators.
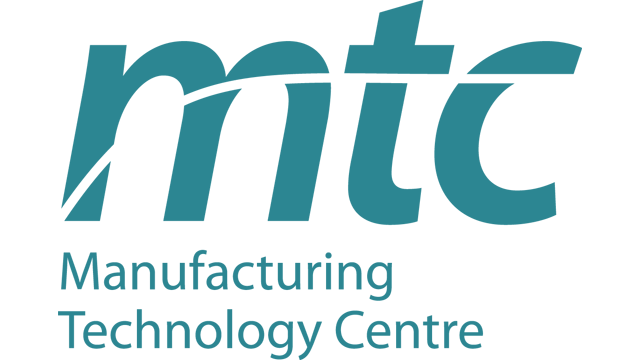
As part of the High Value Manufacturing Catapult, the Manufacturing Technology Centre was called on to support the incoming inspection of parts when other resources were not available. MTC provided quality teams who provided over 700 hours of inspection time.
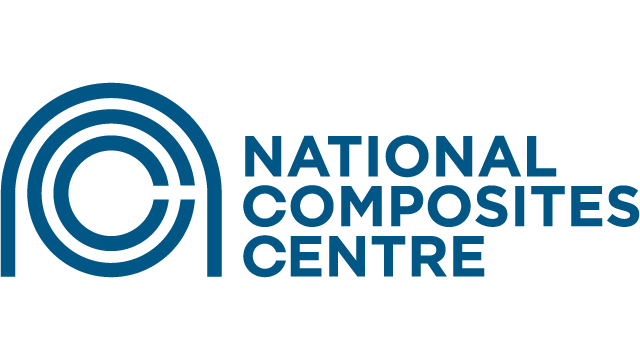
As part of the High Value Manufacturing Catapult, the National Composite Centre were called on Saturday 4th April when it was clear that the inspection team in Solihull did not have the capacity, or some cases the technical capability to cope with incoming parts inspections. By Monday 6th the NCC had 100 volunteers, 20 of whom deployed to cover the operation 24/7 for a month until the peak had been managed and the operation transitioned to Bedford.
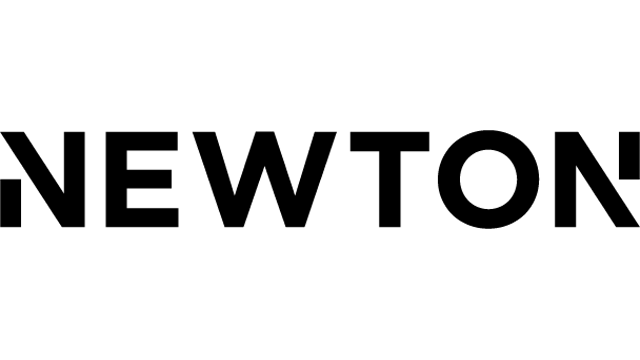
Newton Europe, the UK's fastest growing operations consultancy, has supported Penlon to significantly increase ventilator production as part of the Ventilator Challenge UK consortium. Newton supported with rigorous programme management and critical path identification, high-volume manufacturing realisation plans and aligned multiple sites across multiple workstreams. Working with key stakeholders across the country, from front-line workers to the programme board, Newton were focused on fixing issues before they could impact getting ventilators to the NHS. Newton's expertise in operational excellence, supply chain mobilisation and transformation programme management has played a pivotal role. From identifying the fastest route to regulatory sign-off to driving urgency behind critical tasks, and unblocking the rate limiting processes needed for high volume manufacture, Newton have helped smooth the way for multiple factories to build at pace. For example, when Newton applied their approach to identifying the production network's true constraints, they found a specific test process which could have slowed down the whole system's output. Newton quickly stood up a team who studied the test process in detail, and with no additional labour or upskilling, re-organised workflows to significantly improve capacity - all within a matter of a few hours. Newton's expertise and ability to drive change was a central part in ensuring that the Penlon ESO 2 device was the first emergency ventilator to reach UK hospitals.
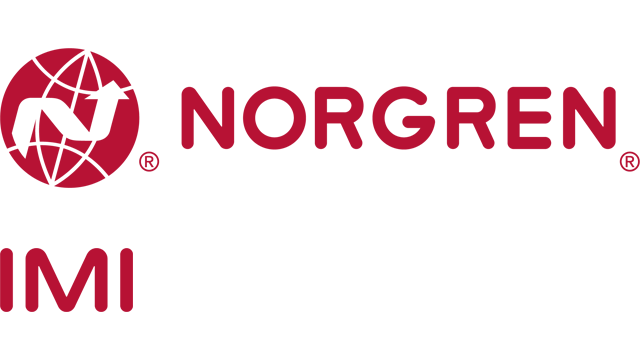
Norgren, part of IMI plc, has been heavily involved in supplying several critical parts to the Ventilator Challenge UK and rapidly adapted its manufacturing facilities to support the project. At its UK Fradley site, production of its RM1 Pressure Regulator was specifically escalated 10x to meet the demand from both Smiths and Penlon. In Switzerland, production of its FAS FLATPROP valve - an essential component which delivers high precision proportional flow control to enable the precise control of very low or high flow rates - was also increased to meet the demand, as well as support consortiums worldwide. The line was previously semi-automatic and has now been transitioned to a fully automated line allowing the site to produce up to 10x its originally capacity per week. Norgren's technical team also played a vital role in working with the consortium in developing specifications and addressing technical enquiries.

The Ventilator Challenge UK consortium is proud to have such a renowned medical technology business at the very heart of its team. Penlon, a long-established medical device company, was one of the two specialist suppliers uniquely well positioned to help in this national effort. Penlon, as the core technology and product owner, has played a central pivotal role within the consortium with its engineering, regulatory and domain strength. The scale and resources of the wider consortium has allowed Penlon to super-scale the production of its Penlon ESO 2 ventilator, the clinicians' number one choice device for the RMVS. The business has converted its entire site in Abingdon to critical end-of-line testing before the ventilators are delivered into the NHS, and in a matter of weeks went from 55 employees in production to 462. The wealth of knowledge, experience and expertise found within Penlon has been critical in supporting its consortium sub-assembly partners including Airbus and Ford, with skilled technicians being on hand to provide real-time technical support through the use of Microsoft HoloLens 2.
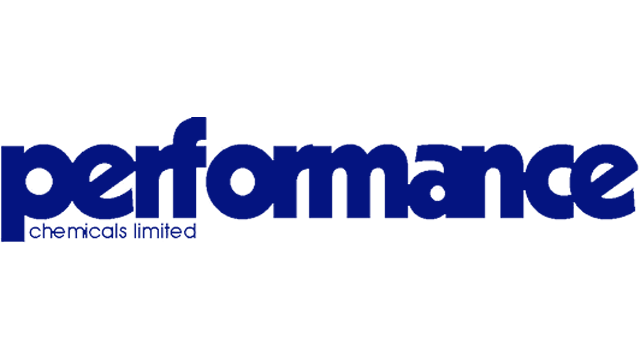
As the chemical CMS for Ford Motor Company, Performance Chemicals, were tasked with sourcing the chemical requirements for the ventilator project. Greases, adhesives, solvents, and silicon sealants. They used their knowledge of key manufacturers and suppliers to pull in required products within a few days of the request.
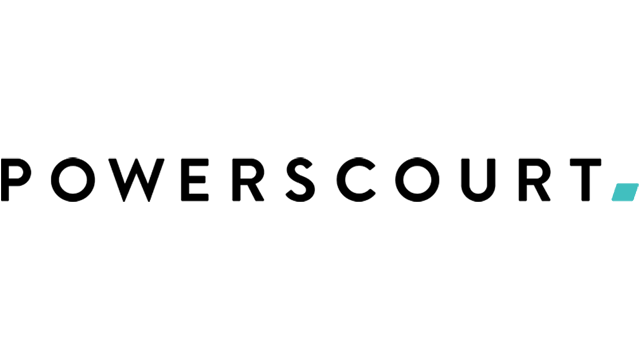
Powerscourt is a multi award-winning communications consultancy, with offices in London and Dublin. It specialises in advising clients on financial and capital markets communications, corporate communications and campaigns, political and regulatory affairs, and crisis communications, backed by deep industry sector expertise. Its 60 consultants draw on the experience of former journalists, industry specialists, equity analysts, bankers, researchers, accountants, and career communications professionals. The firm has been providing wide-ranging communications support to the Ventilator Challenge UK consortium since it was formed in March, having first become involved through its client Airbus which is one of the group's members. Led by James White and Jack Holden, the team has advised on large aspects of the group's communication strategy, supported with a number of the media activities organised by the consortium, and managed the press office for UK and international media. Working with the heads of communications from the consortium's many members, it has also helped to devise the broader media approach to ensure that the outstanding efforts and achievements of the individuals and businesses involved are duly recognised.
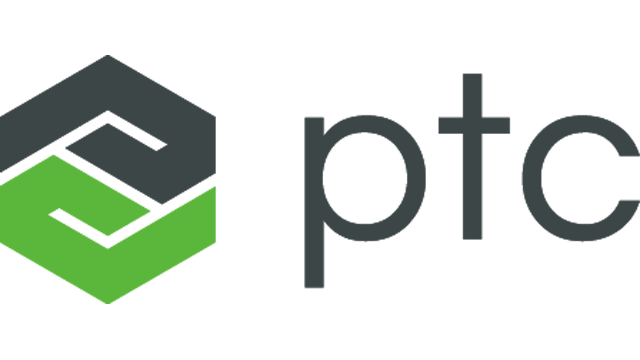
PTC, using Vuforia Expert Capture, captured the entire build process for the two different ventilators (designed and manufactured by Smiths Medical and Penlon) using Augmented Reality and a worker wearing Microsoft HoloLens 2 glasses. This information rich content was then transferred to the Microsoft Azure Cloud and edited in PTC's Vuforia Editor technology, with trouble-shooting instructions added to overcome especially complex stages. The build process was then delivered to the consortium partner factories using Augmented Reality where a manufacturing professional put on the HoloLens 2 and completed the ventilator build. Simply put, adopting this approach reduced the lead-time to get assembly teams productive and delivered improved consistency on the factory floor. And critically, consortium teams avoided the potential transmission of COVID-19 as they removed the need to insert Smiths Medical or Penlon experts into new partner factories.
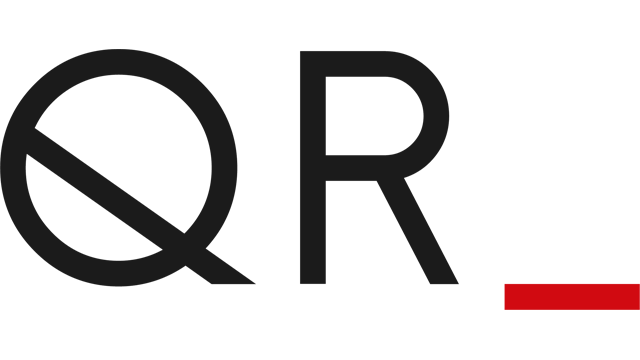
QR_ are product data management (PDM) specialists improving the flow and quality of data and parts through the Penlon ESO 2 ventilator supply chain and manufacturing process. Data quality - the extent engineers' intentions are reflected in production realities - was maximised through proactive bill of materials (BoM) attribute management. Reworking issue management processes for faster resolutions enhanced forward visibility for purchasers and suppliers, minimising wastage and time lost to retooling. Exhaustive supplier chasing, close systems and process integration with logistics providers, and tighter scrap management further enhanced data quality and proved a key enabler in sustaining the heightened operational tempo. Optimising data flow - information's movement through the consortium's digital plumbing to the right person at the right time - further supported impactful and timely decision making. Inside a week, QR_'s Special Projects team scratch coded a material requirements planning (MRP) tool providing consortium-wide access to part-level stock and supply forecasts relative to the agreed production schedule. Establishing a central helpdesk and creating an operational handbook contributed to speedier cross-consortium working. Devising and delivering assembly training materials equipped a skilled but unfamiliar workforce with the knowledge necessary for achieving the ambitus production ramp. Ongoing multi-site quality assurance work drove continuous improvement further underpinning series production.
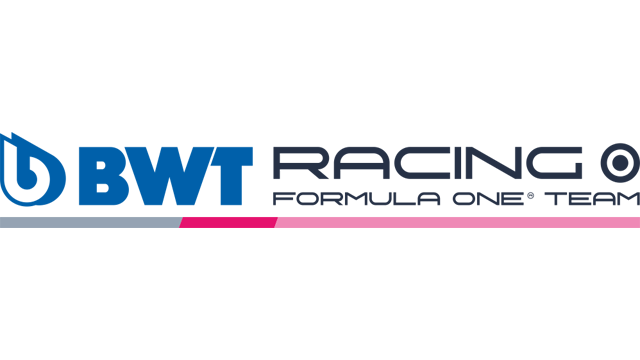
A huge response from the staff saw more than 80 volunteers put their names forward for consideration to support this challenge. The skills of the workforce were especially suited to inspection, testing and sign-off of ICU ventilators. 35 volunteers were therefore placed at Penlon near Abingdon, tasked with final inspection duties during April and May.
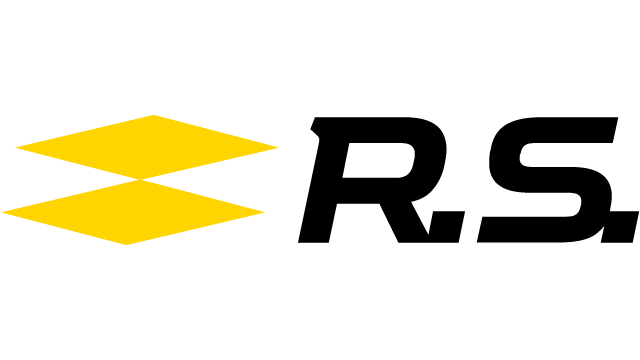
More than 150 Renault volunteers contributed to the ventilator project assisting with machine testing, PAT testing, approval, logistics, management, risk assessment, PHSE and other essential workstreams.
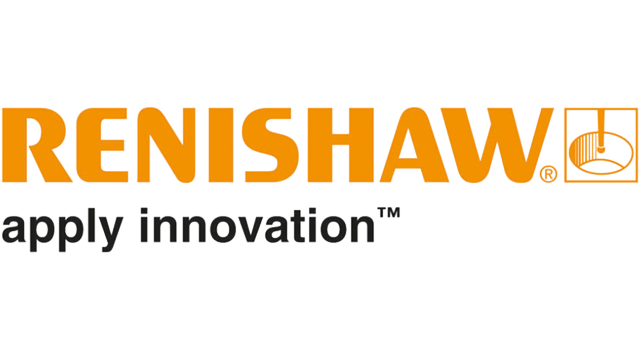
Renishaw is one of the world's leading engineering and scientific technology companies, with expertise in precision measurement, metal 3D printing and healthcare. It employs over 4,500 people worldwide and supplies products for use in applications as diverse as jet engine manufacture, dentistry, and brain surgery. The company was initially approached by the Cabinet Office and having judged that its best contribution would be to help existing device manufacturers ramp up their production, joined with those of a similar mindset to form the Ventilator Challenge UK (VCUK) consortium. Renishaw's main contribution was the manufacture of parts for both the Smiths and Penlon ventilators, producing 115,000 machined components at its sites in Gloucestershire and South Wales. It also carried out the early analysis of the Smiths bill of materials to identify suitable machining processes, helped in the identification of machining supply chain options through liaison with machine suppliers and trade associations, and gave metrology support to other consortium members. The company was able to rapidly ramp up production of 16 ventilator components in a 24/7 operation due to standardised tooling, proven fixturing and in-house developed machining platforms that incorporate automated work handling and the company's own measurement probes.
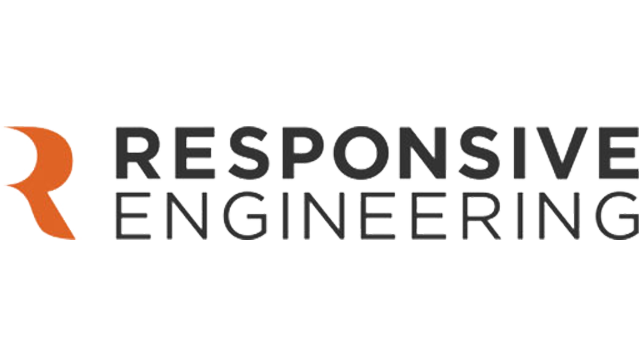
Responsive Engineering Limited (REL) specialise in complex machining and fabrication work for the energy and rail sectors and are seen as one of the UK's major defence manufacturing suppliers to many of the UK's defence prime contractors. REL were approached by McLaren Racing on the 28th March 2020 to manufacture various engineered parts for the VCUK program and issued the first quotation within 2 days of RFQ receipt and received the first PO for the brass cell location plates on the 31st March 2020. REL successfully manufactured and delivered almost 10,000 components to McLaren all of which were a critical part of the Penlon ventilator system.
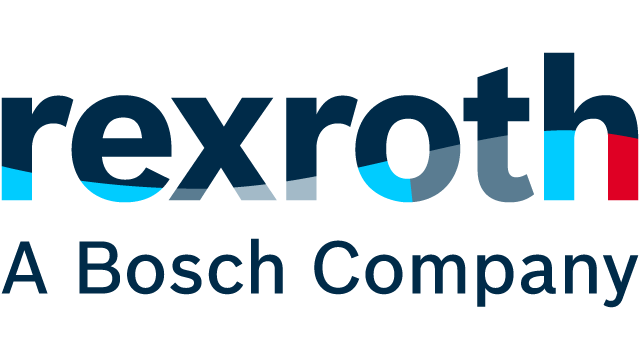
As a leading supplier of automation with a large portfolio and extensive production experience, it was no surprise that Bosch Rexroth was asked to join a group of suppliers providing key technology and expertise to members of the Ventilator Challenge UK consortium. On the one hand, we were asked by Ford to assist its team with the design and setup of a system able to guide untrained operators through a complex lengthy test sequence for the rapidly installed production of ventilators at its facility in Dagenham. Within 10 days, the Rexroth team had designed, demonstrated, modified, quoted, ordered, and built 44 new Operator Guidance Systems as well as reconfiguring 18 systems borrowed from another automotive end user. Due to the intuitive software, flexibility and ease of use, the customer was able to continually improve its own process with minimal support from Rexroth. The second part of the project involved supplying ventilator trolley kits to McLaren, who were responsible for the production of the trollies. Rapid sourcing of the parts, great teamwork, and quick turnaround from design to production ensured that Bosch Rexroth was able to supply the required number of kits within a short time. In total, Bosch Rexroth supplied around 40km of aluminium (15,100 sets) within seven weeks, manufactured at its facility in Cirencester.
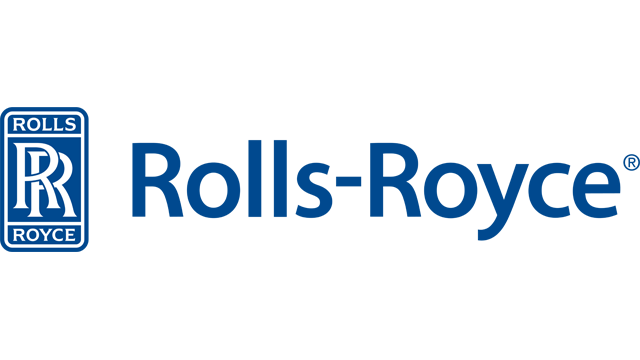
Rolls-Royce worked with Smiths Medical and GKN Aerospace to scale up production of the Smiths paraPAC plus™ ventilator, which has been used by the NHS for more than a decade. Their role has been to create a supply chain from scratch, sourcing supply of the 292 components that make up the ventilator, from 121 different suppliers. They sourced 3.4 million of these parts, which were sent to production lines around the UK, where the ventilators were assembled. One of these production lines was built from scratch at their own site in Bristol. In total, 300 Rolls-Royce employees worked on the challenge.
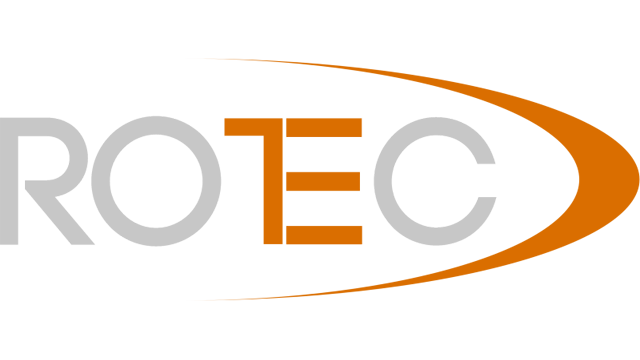
Rotec Engineering Ltd produce diverse subcontract parts, at a rapid turnaround time, for many industries around the world including Automotive, Aerospace, Medical, Military and Agriculture. They retooled and diversified to produce 250,000 medical parts in the space of 3 weeks for the Ventilator Challenge UK.
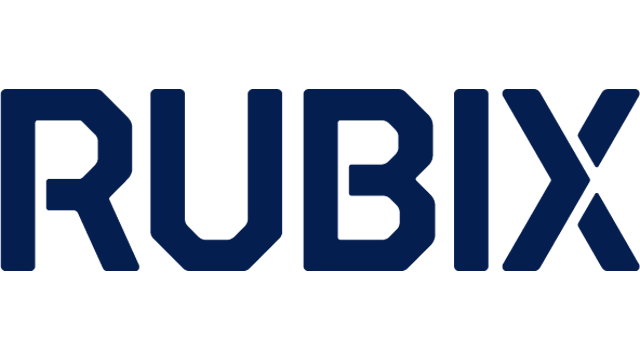
Working with precision engineering business Nasmyth, Rubix - Europe's largest distributor of industrial products and services - produced critical components for the ventilators, designing a cutting application and manufacturing the bespoke cutting tool inserts within 24 hours. At another production site, a Rubix team sourced a vital grease when it looked like a supply shortage was going to cause a production delay. Teams across Europe responded to the internal request for stock within minutes. The full quantity was sourced and delivered within 24 hours, enabling ventilator production to remain on schedule. Elsewhere, Rubix helped the consortium prepare for manufacturing to begin, supplying products ranging from specialist chairs for the engineers through to PPE and bespoke torque gauges that were air freighted from the USA. Rubix also established a regular replenishment cycle to ensure the right products are available throughout production.
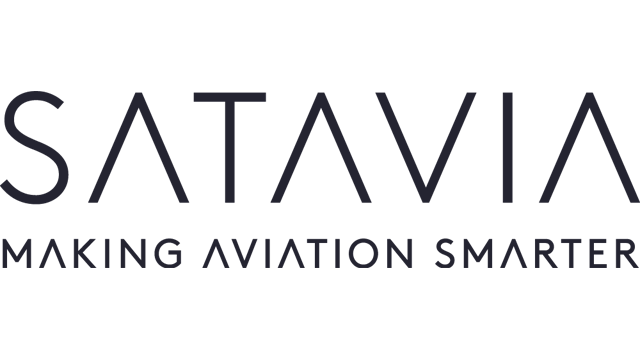
Cambridge-based (UK) SATAVIA has been applying its data scientist expertise in the fight against COVID-19. SATAVIA data scientists rapidly developed forecasting models for the COVID-19 pandemic to predict how many ventilators could be required at the peak in the UK and USA.
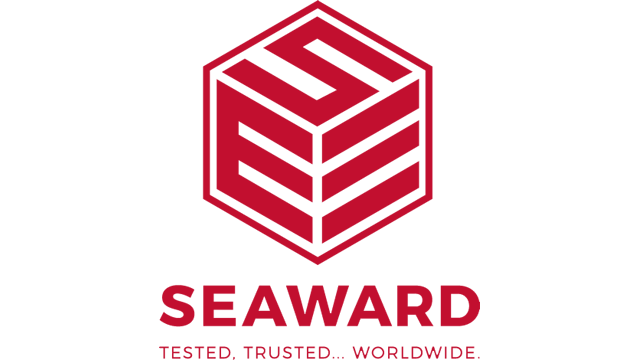
North East manufacturing firm Seaward supplied vital electrical safety testing equipment to the new Nightingale Hospitals and existing hospitals across the UK, as well as internationally. Seaward builds electrical safety testing equipment for everything from ventilators to hospital beds, hoists, and pumps via its medical arm, Rigel Medical. Andrew Upton MD of Seaward, said: "A limited workforce is keeping the Peterlee-based factory up and running. The greatest call at the moment is for the electrical safety checking of ventilators. Because a lot of the equipment is either brand new or older and being brought back into use, it is vital it is safety tested to protect patients and staff. We are supplying to the UK and the rest of the world and our team is working flat out to cope with demand. We see it as our way of being able to say 'thank you' to the NHS. We have been working on behalf of the Cabinet Office commissioners to supply products to Nightingale Hospitals and through firms such as Mercedes, Ford, Rolls-Royce, Dyson, and McLaren who are also part of the effort. Although it has been hectic, and we have been producing and selling five times as much of this type of equipment, we have had to abandon everything else for the time being to concentrate of what is so urgently needed.
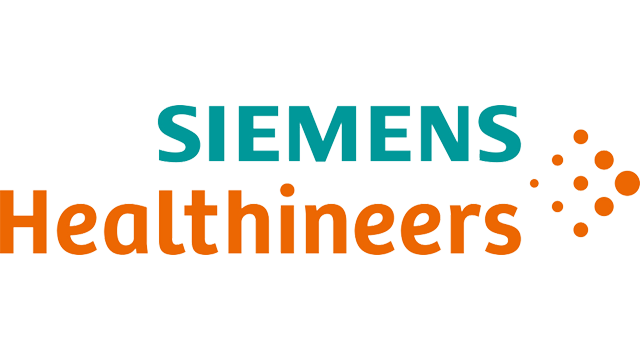
Siemens Healthineers is an established provider of medical devices and software solutions to the NHS with longstanding manufacturing and R&D facilities in the UK which have MHRA accreditation. The products they manufacture here such as blood, gas analysers are designed for use in A&E and critical care so the experience, medical expertise and industry knowledge from Siemens Healthineers is vital to the consortium. Siemens Healthineers drove the quality system focus across both streams for the first 7 weeks. Once Smith's had a stable position and plan, they focused fully on Penlon. Siemens Healthineers worked with Penlon to bring 180 new suppliers into Penlon's QMS. This included desk top assessments, audits as well as a few sites visits at short notice. The joint team developed and supported the training plan for all operatives (circa 5000) across the programme to ensure consistent quality. This was key as the majority of the other partners involved weren't used to working in this type of regulated environment. As production ramped up the team worked together to release the products reviewing the DHR's to again assist in the quality messaging and consistency. For each machine, the documentation pack is just as important, and the number increase is the same. To make this even more efficient the team, supported the implementation of an EDHR system across all sites in record time, to improve the DHR First time pass rate and increase capacity in the system. Siemens Healthineers expertise helped bring quality to the front of the Consortium which included input in the strategy to gain MHRA approval of the ESO2.
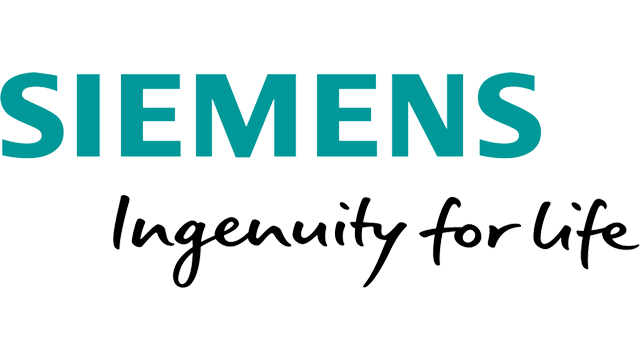
At the AMRC Wales, Siemens worked with Airbus and team members from Penlon on sub-assemblies for Penlon's Prima ESO2 device on two of the Penlon Prima ES02 sub-assemblies - the breather absorber and flow meter. Using their knowledge of electro-mechanical device manufacturing from Variable Speed Drives in their Congleton factory and Industry Software tools, they designed, validated, and delivered two distinct sub-assembly manufacturing lines in three weeks. These lines were both replicated eight times to reach target production capacity. This was achieved using a digital twin approach, whereby the Production System was designed remotely without sight of the physical product or plant.
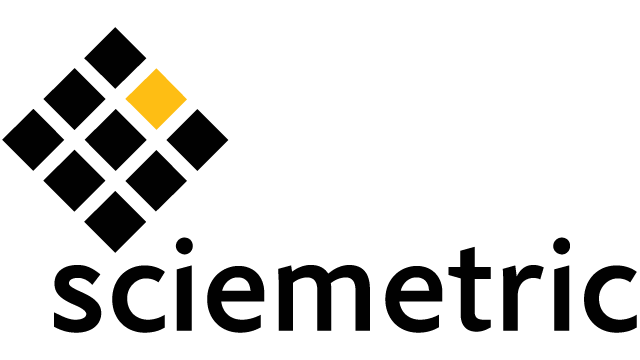
Sciemetric was approached with this urgent request on a tight timeline, and Sciemetric's team across the UK, Canada and the US worked together to make it happen. Sciemetric was tasked to build 5 new workstations to test the new ventilators. The new workstations employ Sciemetric's sigPOD to test for product quality and reliably identify any faulty parts to ensure all ventilators shipped to health care facilities across the UK perform optimally, as intended.
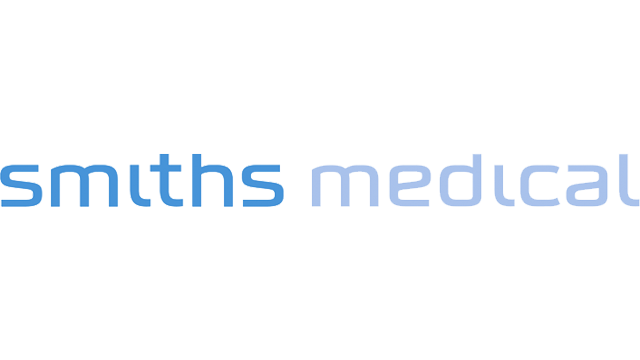
The Smiths paraPAC plus™ ventilator is a mechanical, mobile device originally designed by Smiths in 2008. The device has been used to help save lives by ambulances and hospitals in the NHS and overseas for more than a decade. Smiths oversaw the overall programme management and workstream integration for the production of the Smiths paraPAC plus™ ventilator. They scaled up production at their Smiths Medical site in Luton from 20-30 ventilators a week to hundreds a week and have worked closely with other consortium members including GKN and Rolls Royce to add additional lines in their facilities thereby adding significant capacity to the production of the Smiths paraPAC plus™ ventilator. Quality control and assurance was paramount throughout the manufacturing process and the Smiths Medical team at Luton supported the commissioning of new test boxes, essential to the production process, for the additional production lines.
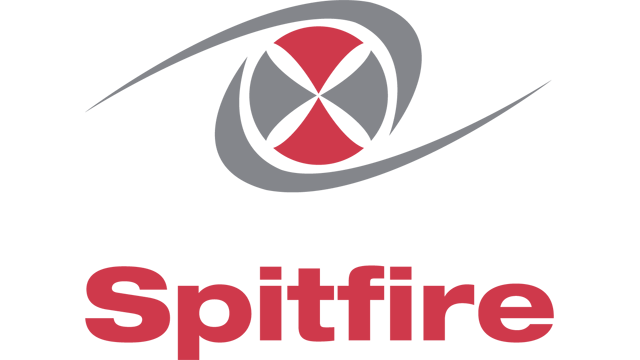
Spitfire were engaged in the Ventilator Challenge UK programme to help to develop the pop-up production lines for one of the lead consortiums via the utilisation of their vast high-volume manufacturing experience coupled with their innovative training processes and materials. They assisted with production line balance and quality critical operations design and progressed to the writing and implementation of robust Work Instructions for every critical operation. They then deployed their unique interactive Visual Manual technology on key operations to assist with accelerated learning for the many new staff that were deployed onto the production line in this high-pressure situation.
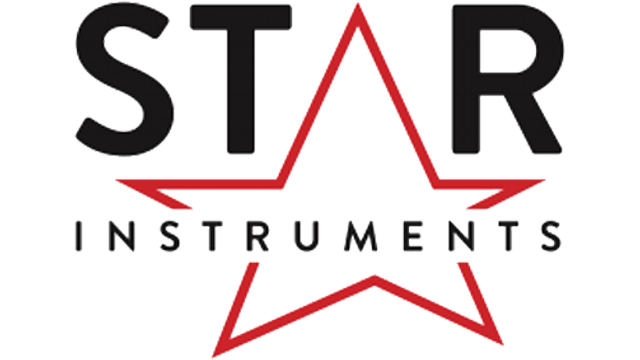
Star Instruments received information from Project Pitlane, via the McLaren Group, and Ford Motor Co., and immediately set to work in modifying its existing Pressure gauge design and manufacture, to ensure they were oxygen compliant, for Ventilator applications. A number of 'oxygen clean' prototype gauges were developed within days and sent to the consortium for approval. Star Instruments then supplied production gauges for both McLaren Woking site and Ford Motor Co Dagenham Engine Factory. With one such supply agreement in place with this consortium, Star Instruments where then immediately contacted by a second group within Project Pitlane, this time from Williams Advanced Engineering. Star Instruments then started producing a number of specialised pressure gauges to test the Smiths paraPAC plus™ ventilator at Williams Woking factory and at Smith Medical Group.
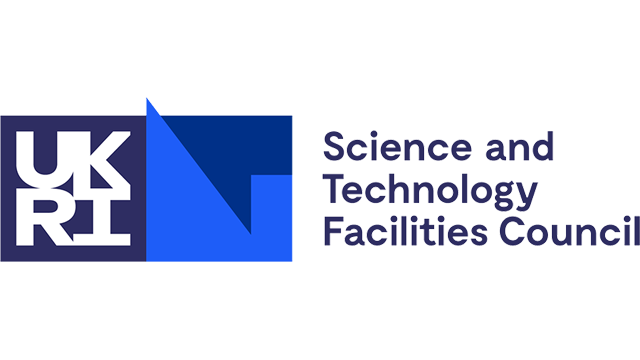
Technicians from the Science and Technology Facilities Council (STFC) Rutherford Appleton Laboratory at Harwell led the training of a team of around 300 in testing and calibrating the ventilators produced by Penlon at its facility in Abingdon, Oxfordshire. These same technicians were then part of the team testing the ventilators and providing logistics services, working over six shifts. Over 70 members of staff have been involved, from apprentices to particle physicists. The team used the skills and expertise gained from making and running the international scientific research facilities at Rutherford Appleton Laboratory.
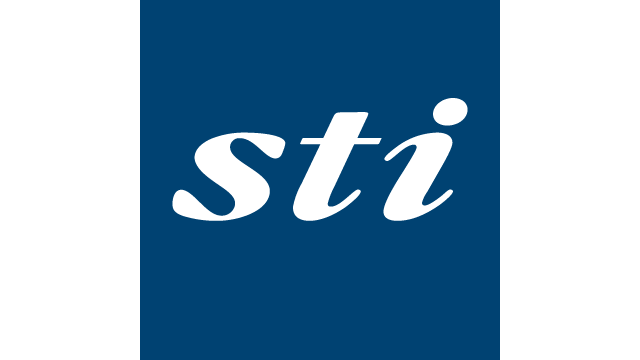
Surface Technology International (STI) Ltd is a specialist Contract Electronics Manufacturer (CEM) serving world-class customers in high-reliability industries, providing electronics design and manufacturing solutions in both printed circuit board assembly (PCBA) and full box-build manufacturing. STI was responsible for the final assembly of the Penlon ventilator and had a team of 70 production staff working on the project at its facility in Hook, Hampshire. STI was also involved with the production of the Smiths Medical ventilator, producing PCBAs for ventilator test equipment.
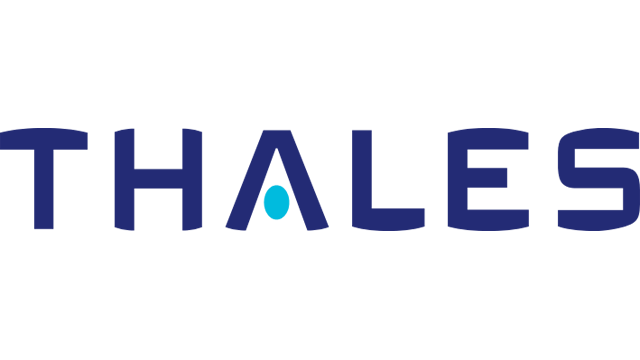
Thales has leveraged its strong capability in safety critical training and electronics in order to support the Ventilator Challenge UK Consortium. Thales' main role was in leading the Smiths consortium training work stream, working closely with Smiths Medical (OEM) and GKN; managing a broad team of industry and technical experts to develop key training materials, including Assembly Operator training and Clinical Operator Training. Thales also took responsibility for supporting specialist supply chain issues, sourcing, and manufacturing printed circuit board assemblies (PCBAs) and associated hardware to support the manufacture of larger numbers of Smiths ventilators, working with Rolls-Royce. This included increasing capacity of the current supply chain and working with additional suppliers to create second sources of supply to minimise risk across the supply chain.
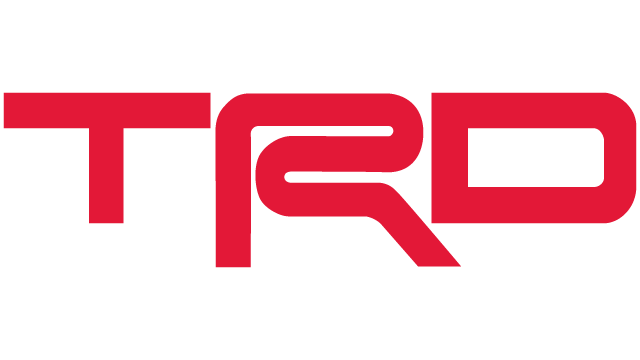
TRD USA (TRD), Toyota's North American motorsports engineering arm was contacted via a mutual connection by the Ventilator Challenge UK consortium at the end of March looking for support for Spiracle Technology, a local (to TRD) southern California based manufacturer of medical ventilator demand valves. The valves are used in a Smiths produced medical ventilator. After introducing themselves to Spiracle and understanding their needs and challenges, TRD offered to repurpose some of their design, engineering, manufacturing, and production engine build resources to support increased production throughput for Spiracle. Over the course of approximately five weeks, TRD procured, sourced, and manufactured the components and hand built twelve end-of-line ventilator valve test rigs for Spiracle and the consortium (Spiracle only had one test rig on-hand). Additionally, TRD team members provided Spiracle valve assembly and sub-assembly support from their Costa Mesa facility. TRD directly supported the assembly of over 2000 ventilator valves and thousands of sub-assemblies, normally a two-year production quantity. TRD designed and provided Spiracle with custom build tooling, documented the assembly process for and provided supply chain management tools to support greater efficiencies and production throughput going forward. In total, approximately 4900 TRD man-hours amongst 50 team members were donated to this initiative.

ULTRA's contribution to Ventilator Challenge was advising and contributing to the supply chain challenge especially in relation to electronics, assemblies, and components. They have worked primarily on the Penlon unit where the Automatic Ventilator System has a number of bespoke assemblies of electronics on multilayer circuit boards. In order for production to be extended to the numbers required by the UK Government components had to be sourced sometimes to their nearest equivalent in order to stay within the strict quality requirements. ULTRA has significant industry experience in addressing Electronics design for precision systems such as the Penlon unit. Across ULTRA is a commitment to quality and conformance to standards across many disciplines that are highly regulated. ULTRA also advised on matters of final testing and acceptance.
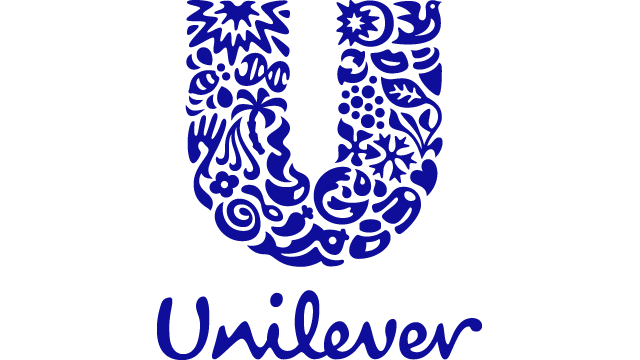
Unilever's contribution included sharing their technical expertise, as well as helping to engage their own partner network with the consortium. They also provided PPE, including gloves and masks, and essential food, surface cleaner and hygiene products to support the facilities within the consortium who manufactured the ventilators and parts.
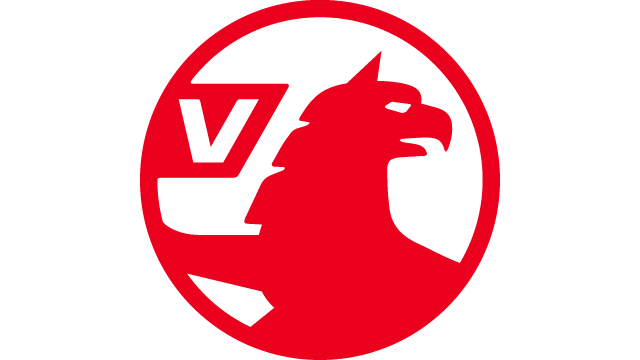
On 9th April, workers from Vauxhall's Luton plant downed their regular tools in favour of slightly more clinical surroundings to meet huge NHS demand for ventilator production as part of the Ventilator Challenge UK. Vauxhall provided 22 staff to the Luton site of Smiths Medical. The staff - 20 assemblers, plus a Team Leader and Supervisor - were hand-picked from Vauxhall's Kimpton Road Plant that produces the Vivaro van. They were chosen due to their specialist skills and ability to carry out intricate production work to a very high standard.
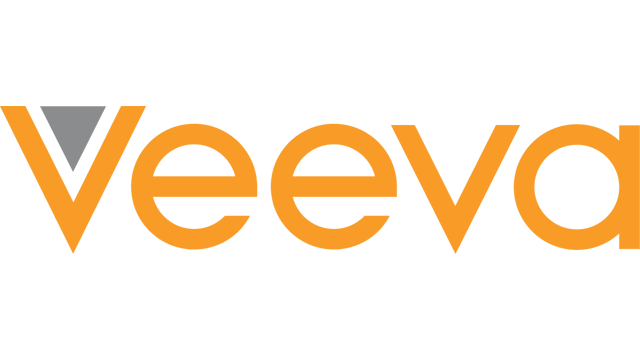
Veeva partner with the Ventilator Challenge UK consortium to provide its Vault QMS solution to enable global management of the quality process across all manufacturing sites in the Penlon consortium.

Supplied cleaning machinery free of charge to the Dagenham site.
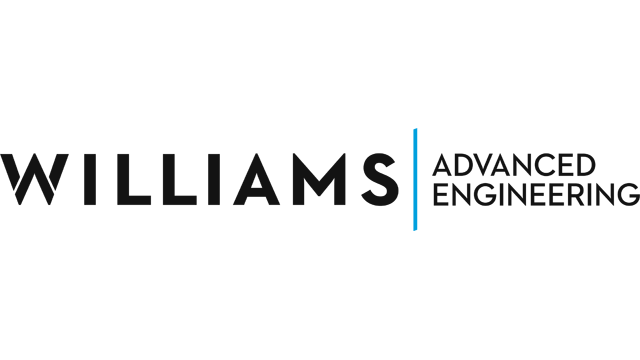
Commencing on the 19th March, Williams Advanced Engineering (WAE) and Williams F1, working alongside Renault F1 and Mercedes F1, undertook the rapid design, production and sourcing of a significant number of prototype components to facilitate the pre-production build and validation of the Smiths paraPAC plus™ ventilator. Following this, WAE and Williams F1 went on to support the rapid manufacture of a number production tools and test boxes, having initially scanned and reverse engineered these. Williams' combined efforts over the initial 5 weeks of the project assisted the consortium in being able to replicate the Smiths paraPAC plus™ ventilator production line, and thus increase production rates.
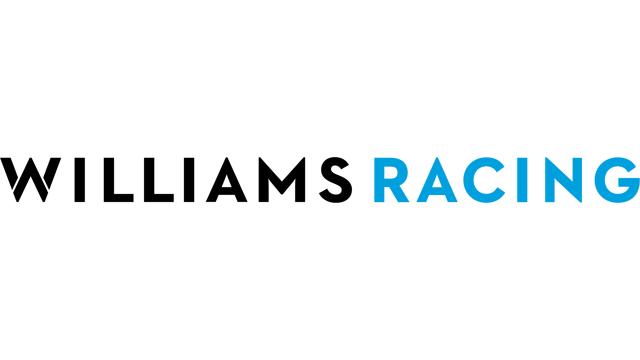
During the last few days in March Williams F1 working with Renault F1 and Mercedes F1 undertook the rapid production and sourcing of a significant number of prototype components to facilitate the pre-production build of the Smiths paraPAC plus™ ventilator. Following this initial phase Williams F1 then went on to support the rapid manufacture of a number production tools which had been reverse engineered by Williams Advanced Engineering. This assisted the consortium in being able to replicate the Smiths paraPAC plus™ ventilator production line. Williams F1 also provided a number of staff to support the Penlon production phase at their Abingdon site. The number of Williams F1 volunteers far exceeded the actual numbers required. In total 112 Williams F1 staff members were trained with the majority rostered onto the shift pattern. The remaining volunteers were on standby to ensure no shift patterns were left short.
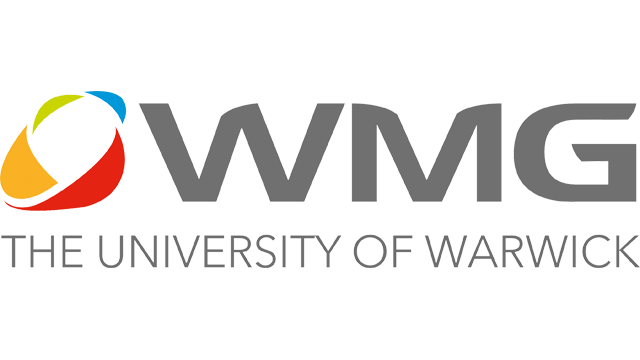
As part of the High Value Manufacturing Catapult, WMG was called on to support the incoming inspection of parts when other resources were not available. WMG provided 10 people to cover inbound quality inspection.
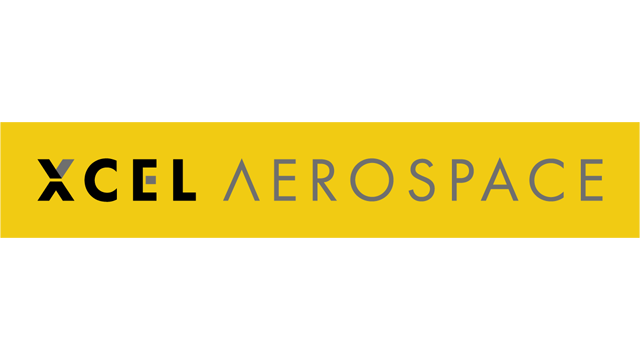
XCEL Aerospace proudly supported Rolls Royce in the manufacture of components for ventilators. The Xcel team rose to the challenge, receiving the initial call on a Friday afternoon, receiving the drawings on the Sunday, and delivering parts by the Thursday. This ensured they were able to deliver in excess of 4,000 parts within 5 days.
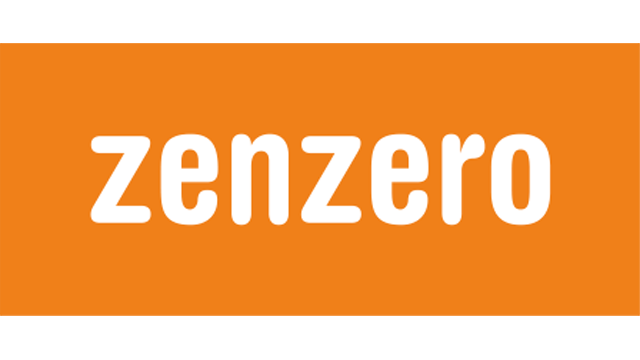
Zenzero's IT team managed the IT central infrastructure which was housed on HVM Catapult's cloud platform. This allowed members of the consortium to share interactive guides, access crucial production information and design work and manage the supply chain of the project.