Return material adjustment (RMA) processing through the mobile device
This blog post assumes a working knowledge of the new Warehouse management module released in Microsoft Dynamics AX 2012 R3.
The process of receiving a Return material adjust (RMA) using the new WMS mobile device functionality is very similar to processing an inbound transaction such as a purchase order. The following steps are intended as a walkthrough of the necessary setup and actions required to complete the process. They are completed against the USMF Contoso dataset on a CU8 installation.
1) Set up a Return order work template
- Warehouse > Work > Work Templates
- Change the Work order type to “Return orders”
- Create a new work template by clicking the New (figure 1)
- Create new work type lines by clicking the New button on the low section of the grid
- Create two lines (figure 2)
- The first
- Work type = Pick
- Mandatory = Checked
- Work class ID = Return
- The second
- Work type = Put
- Mandatory = Checked
- Work class ID = Return
- The first
- Close the form
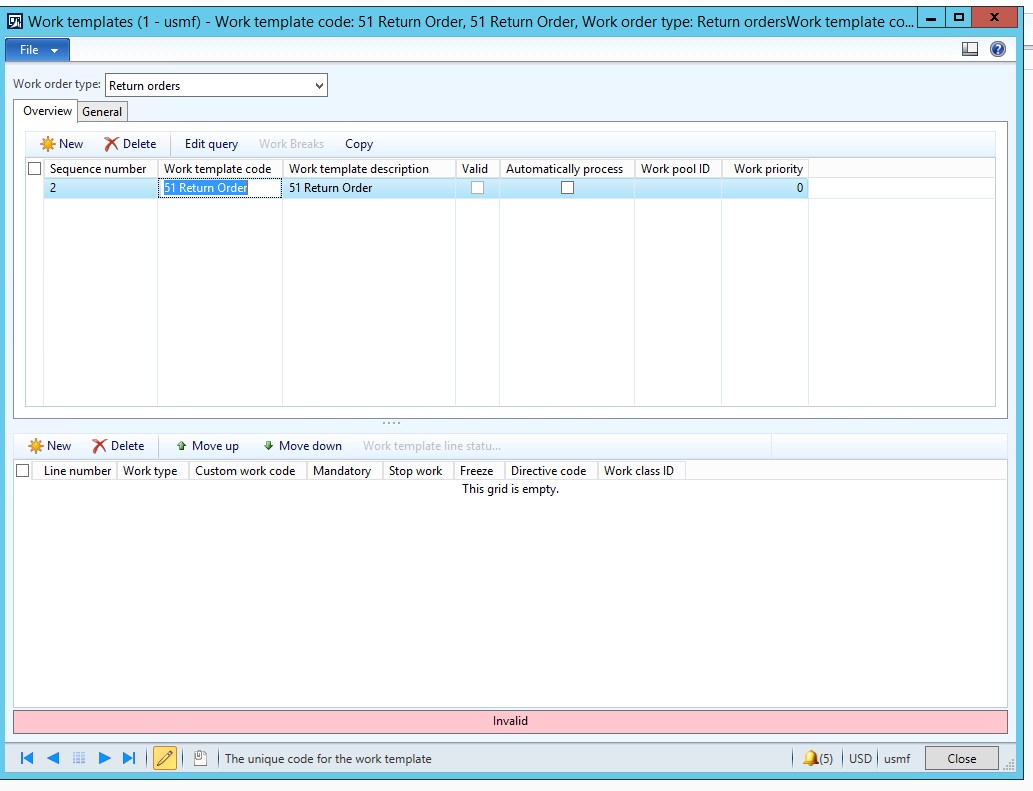
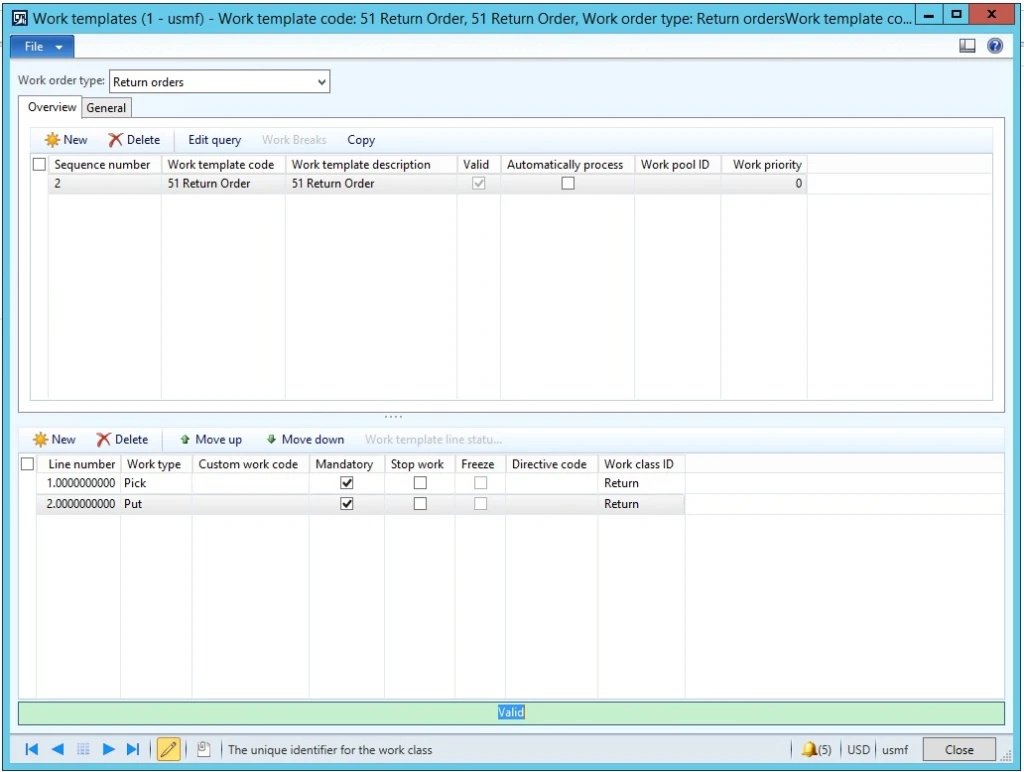
2) Setup a Disposition code and link it to an inventory status
- Warehouse management > Mobile device > Disposition codes
- Create a new Disposition code by clicking the New button
- The new Disposition code will need the following fields
- Disposition code: The name of the disposition code.
- Inventory status: An inventory status which will define the blocking strategy assigned to the returned item.
- Work template code: The work template to which this disposition code should be linked.
- Return disposition code: A traditional disposition code that contains the disposition action.
- Note: Any disposition code that has an action of “Return to customer” will not generate work as of CU8
- Create the record with the following values
- Disposition code = Customer return
- Inventory status = Available
- Work template code = 51 Return Order
- Return disposition code = 11
- Close the form
3) Create a location directive to manage the Return order process in the warehouse
- Warehouse management > Setup > Location directives
- Change work order type to “Return orders”
- In the Location directives fast tab click New
- Sequence number = 1
- Name = 51
- Work type = Put
- Site = 5
- Warehouse = 51
- Disposition code = Customer return (the disposition code must be specified or the location directive will not be found).
- In the Lines fast tab click New
- Sequence number = 1
- From quantity = 1
- To quantity = 999,999
- Locate quantity = None
- In the Location Directives Actions Click New
- Sequence number = 1
- Name = Put
- Fixed location usage = Fixed and non-fixed locations
- Strategy = None
- In the Location Directive Actions fast tab click Edit Query
- Set the Location Criteria = Bulk-001
- Click OK to close the form
- Close the Location directives form
4) Create a menu item on the Mobile device
- Warehouse management > Setup > Mobile device > Mobile device menu items
- Click New to create a new menu item
- Menu item name = RMA Process
- Title = RMA Process
- Mode = Work
- Work creation process = Return order receiving
- Close the form
5) Add the new mobile device menu item to the mobile device
- Warehouse management > Setup > Mobile device menu
- In the Available menus and menu items section find the RMA process and add it to the menu structure by clicking the “<” button
6) Create a return order
- Sales and marketing > Common > Return orders > All return orders
- In the panel click Return orders> New > Return order
- Customer account = US-004
- Click OK to create the return orders
- Add a line to the return order
- Item number = A0001
- Site = 5
- Warehouse = 51
- Unit price = 5
- Quantity = -1
- Copy the RMA number on the Return order header (General fast tab)
7) Open the Emulator in the AOT and receive the RMA to create the work
- AOT > FORMS > WHSWorkExecute > Right click > Open
- User ID: = 51
- Password = 1
- In the main menu select RMA Process
- Enter the RMA number click OK
- Item = A0001
- LP = TestLp
- Qty = 1
- Disposition code = Customer return
- Click OK
8) Navigate back to the Return order and open the sales order to view the work
- On the RMA select the sales order number to open the sales order for the RMA
- On the Sales order in the Sales order lines section click Warehouse > Work details
- Notice the work has been created. The pick in the receipt location and the put away is set to the location specified in the location directive