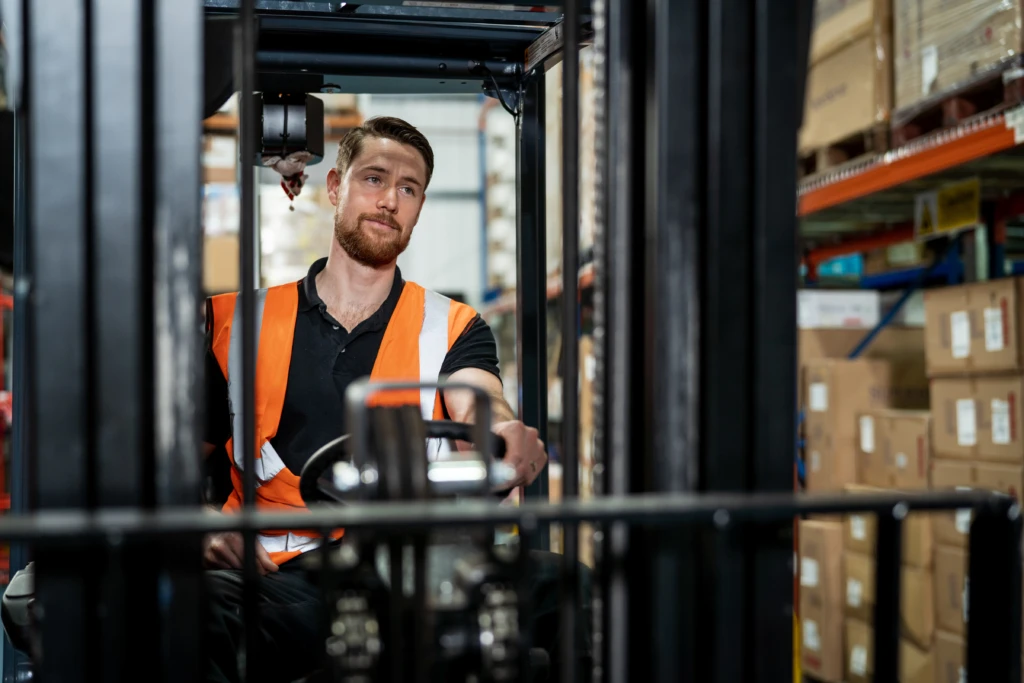
Optimize your supply chain with priority-based planning
In supply chain management, when you have an urgent demand, you want it to be prioritized across your planning system. The ability to enable such a broad, yet flexible factor as prioritization, is now available in Dynamics 365 Supply Chain Management.
Priority-based planning can help businesses optimize their supply chain while increasing service levels and reducing inventory levels. The 2021 release wave 2 includes a public preview of this feature for the Planning Optimization Add-in for Dynamics 365 Supply Chain Management.
Benefits of priority-based planning
This feature adds support for demand-driven planning, which is one of the five steps related to demand driven material requirements planning (DDMRP). With priority-based planning, the optimization of supply to cover demand is based on priorities, not requirement dates, which are used in classic material requirements planning (MRP).
Priority-based planning lets you prioritize replenishment orders to ensure that urgent demand is prioritized over less important demand. For example, a stockout replenishment order will be prioritized over a standard refill replenishment order.
On top of this, the system can automatically split large refill orders into separate, smaller orders, with different priorities assigned to each order. This approach provides coverage of the critical portion of an inventory refill, instead of simply refilling warehouses to maximum with a single supply. This minimizes the risk of stockout by optimizing the use of available supply.
Another benefit of priority-based planning is that priority can be used to compare the importance of relevant orders across products and locations during execution planning.
Broad impact of the planning priority value
The new field, Planning priority, is now available for purchase orders, sales orders, transfer orders, planned orders, and forecast lines. This value is the backbone of priority-based planning; it is used to define the importance of demand and supply.
Planning priority is typically defined by the master planning calculation related to a planned order, or by a default value when manually created. Users can modify the planning priority value when needed. For example, it might be important to adjust the value to honor the importance of a critical sales order. For intercompany orders, the planning priority value is kept in sync between linked purchase and sales orders to ensure transparency of cross-legal entities.
Flexibility with the Priority coverage code
By using the new coverage code of Priority, you can control when Planning Optimization uses planning priority during pegging. This will calculate the derived planning priority on planned orders based on inventory levels and demand priority constraints.
This addition makes possible a flexible approach with a mix of 1) classic date-driven MRP using coverage codes of Min/max, Period, or Requirement, together with 2) item coverage using the new priority-driven approach defined by use of the Priority coverage code.
Planning priority models
The user-defined planning priority models enable a variety of options. One option is to do a standard DDMRP priority calculation, based on projected on-hand supplies as a percent of maximum (see “% of maximum” in the following graphic). However, another option is to use specific planning priority values, based on priority ranges (see “Zone grouping” below).
With priority ranges, you can also choose to split planned orders according to the priority ranges. This ensures that available supply is distributed based on the risk of stockout. With this approach, you seek to fulfill the demand quantity to reach maximum inventory level by creating multiple planned orders, each with individual planning priorities. During firming, it is possible to group planned orders based on priority to limit the number of actual orders to process.
In supply management, sometimes your projected on-hand inventory will reach a critically low level because less important demand orders are repeatedly delayed. Eventually, this triggers a high-importance supply request. When you enable the Consider demand priority setting, a new planned order supply will never be assigned a planning priority that is more important than the demand that triggered the supply. This lets you balance the importance of supply when refilling stock levels in a supply chain with inventory buffers.
How to get started with priority-based planning
- Enable the Planning Optimization functionality. For more information, see Get started with Planning Optimization.
- In Feature management, turn on “(Preview) Priority driven MRP support for Planning Optimization”. For more information, see the priority-based planning documentation.
- Set up your first planning priority model to control the planning priority calculation and the default value of planning priority on new orders and forecast lines.
- Set up a coverage group that includes your planning priority model.
- Ensure that at least one product includes item coverage with coverage code Priority.
- Add the planning priority fields prominently to relevant forms like planned orders.
- Run master planning and try out the planning priority model setup to see the impact on the calculated planning priority on planned orders.
Next steps
Watch this video about the highlights of priority-based planning: Planning optimization support for priority-based planning in Dynamics 365 Supply Chain Management.